Precast Concrete Formwork Magnets
Precast Concrete Magnets (PC fixing magnetic devices) are essential tools used in various formwork constructions. Precast Concrete Formwork Systems are utilized to secure side formwork and embedded elements in precast concrete systems. Precast Concrete Systems ensures efficient and safe handling of the concrete elements, resulting in faster and more precise construction. Precast Concrete Systems are one of the current developments in building industrialization, and it is extensively employed in the sectors of construction, transportation, water conservation, high-speed rail, road construction, and so on.
The key advantage of using Precast Concrete Magnets is their versatility. They can be used in different types of formwork constructions, including walls, columns, beams, and slabs. Regardless of the shape or size of the concrete element, these magnets provide reliable and strong magnetic force to hold them firmly in place. And the Precast Concrete Formwork Magnets are very easy to use. They are designed with a simple, yet effective, mechanism that allows quick and effortless installation and removal.
Except for their strength and ease of use, Precast Concrete Magnets also offer durability and longevity. They are made from neodymium magnets, which ensure a continuous magnetic force even in harsh conditions. These NdFeB magnets can withstand extreme temperatures, chemicals, and moisture, making them suitable for both indoor and outdoor construction projects.

Benefits of using Precast Concrete Magnets
- Significantly reduce labor and material costs and greatly improve installation efficiency;
- Simple and accurate positioning;
- No need to use screws, bolts, or welding for positioning, which can avoid damage to the mold table to the greatest extent;
- Reusable, long service life and short return on investment;
- The construction site environment and the safety of construction personnel can be greatly improved.
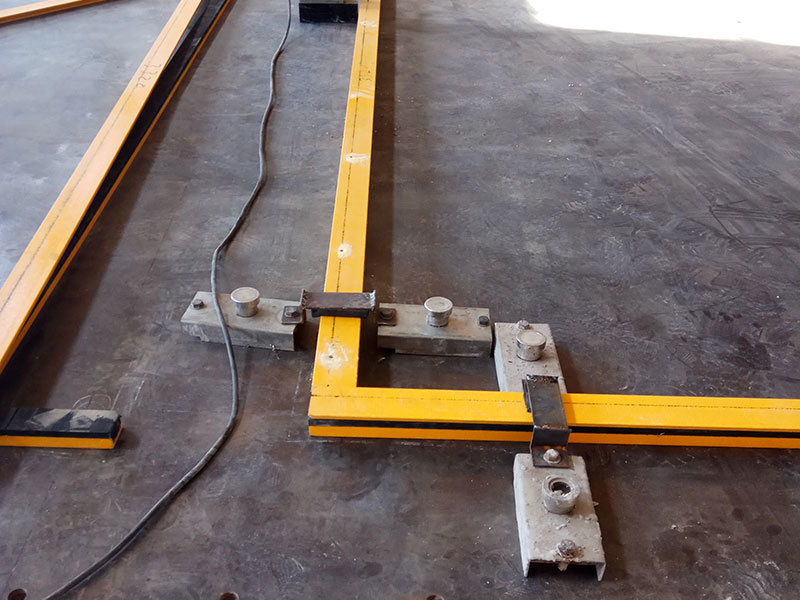
Precast Concrete Magnets are most commonly used as a fixing tool for foundation reinforcement or columns during the construction of beams and columns in conventional construction. In the prefabrication industry, when building the formwork, the reinforcement cannot be directly welded to the formwork, because it will cause the formwork to expand into a concave shape after drying, which will lead to deviation between the actual shape of the formwork and the concrete wall. Precast Concrete Magnets are huge powerful magnet holders with unique magnetic circuits, the magnetic field generated by the Precast Concrete Magnet is very strong, so the two Precast Concrete Magnets posted at both ends of the reinforcement can firmly fix the formwork.
Honsen Magnetics takes pride in our commitment to delivering superior quality and technical excellence. With our advanced production equipment, we are able to manufacture a comprehensive range of Precast Concrete Formwork Systems. Our dedicated team of professionals, equipped with precise testing instruments, ensures that our products meet the highest standards.
1. Shuttering Magnets
Shuttering Magnets are revolutionary tools used in the precast concrete industry. They offer a quick and efficient way to secure formwork to steel casting beds without the need for drilling, welding, or screwing. The template magnet consists of a switchable NdFeB template magnet unit, a housing containing the magnet block, and fixing screws. Through the combination of neodymium magnets and steel plates, a powerful magnetic circuit is formed to generate strong attraction. This force acts to hold the wood or steel formwork in place. The control buttons are located on top of the precast concrete magnets. When the button is pressed, the magnet engages its magnetic circuit, holding the template firmly to the steel plate. Instead, the deactivation button facilitates easy repositioning of the magnet. There are two universally threaded holes on the top of the template magnet, designed to accommodate different adapters. The Shuttering Magnets from Honsen Magnetics can be customized according to your specific requirements, thus providing a diverse use experience.
2. Magnetic Shuttering Systems
Shuttering Systems, also known as Formwork Systems, are indispensable in the construction industry for providing the necessary support and containment for freshly poured concrete. By selecting our Shuttering Systems, you are opting for a dependable and efficient solution to effectively support and contain freshly poured concrete. Our series of Shuttering Systems is carefully designed to meet the varied requirements of different construction projects. Whether it's a small-scale residential development or a large-scale commercial undertaking, our systems are versatile and adaptable to accommodate the specific needs of each project.
At Honsen Magnetics, we prioritize the quality and durability of our Shuttering Systems. Each component is manufactured using high-quality NdFeB Magnets, ensuring resilience and withstanding the demanding conditions of construction sites. We're able to receive tailor-made designs from customers.
3. Insert Magnets
Insert Magnets, also known as Threaded Bushing Magnets or Bushing Fixing Magnets, specifically designed for concrete, play a crucial role in magnetic shuttering systems. They serve the purpose of securely fastening different components and creating form space during the production of reinforced concrete products. With their versatility, these magnets are available in various sizes, effectively reducing labor costs and significantly enhancing both the quality and efficiency of the final products. Embedded fixing magnets are employed in conjunction with the magnet formwork system or steel tables during the manufacturing process of concrete structures. This powerful equipment has enabled precast concrete manufacturers to streamline their daily operations, resulting in time and cost savings. Honsen Magnetics demonstrates our commitment to innovation and customer satisfaction. Our team of experts is dedicated to providing high-quality products to meet the ever-changing needs of the construction industry.
4. Magnetic Chamfer
For many years, Magnetic Chamfer Strips have played a crucial role in the precast concrete industry. They are highly durable and capable of withstanding demanding working conditions. They are primarily employed to attach steel surfaces securely.
Their main purpose is to create beveled edges on concrete wall panels and formwork. The triangle and trapezoid shapes are the most commonly utilized designs for these magnetic strips. Regarding versatility, magnetic strips for precast concrete are unparalleled accessories in the industry.
At Honsen Magnetics, we have various sizes to choose from and we can also customize according to the specific needs of our customers.
5. Shuttering Magnets Adapter
Our Shuttering Magnets Adapter is specifically designed to work seamlessly with our Shuttering Magnets. It provides a fast and efficient way to secure window and door recesses, wood shutters, fiber concrete upstands, and other shuttering elements. We also offer custom services where we can produce adapters to match your exact specifications.
When using our Shuttering Magnets, our adapter ensures high strength and good rigidity. Its special edge tooth design allows for a close engagement with the magnetic chuck, creating a strong coupling. It means that even under external forces, there will be no gaps or loosening, resulting in optimal quality for the final concrete wallboard. As the construction industry rapidly evolves towards industrialization, we are committed to deepening our communication with each customer. We aim to develop and produce high-quality products that meet the practical needs of the domestic market. By doing so, we hope to contribute our expertise and efforts to the construction industrialization industry chain.
6. Lifting Pin Anchors
The Lifting Pin Anchors, also known as the Dog Bone, serves as an essential component embedded within precast concrete walls. Its primary purpose is to facilitate easy lifting during construction. In comparison to traditional steel wire hoisting methods, lifting pin anchors have gained widespread popularity in Europe, America, and Asia due to their numerous advantages, including cost-effectiveness, speed, and labor cost savings.
We're using either cold forging or hot forging techniques, employing 20Mn2 steel as the base material. The surface of the anchors is coated or plated, ensuring that it meets the specific needs and requirements of customers. As the precast concrete industry continues to evolve, lifting pin anchors have become an integral part of the process, working in conjunction with lifting clutches and dog bone recess formers.
Why Choose Us?
Honsen Magnetics specializes in the production of Precast Concrete Formwork Magnets. Our team comprises highly skilled magnetic circuit design engineers and mechanical design engineers who bring their expertise to every project. With years of experience in the industry, we have built a mature team proficient in design, sampling, and batch order delivery.
In addition to our comprehensive design and production services, we emphasize the importance of consistency in our batch products. Our goal is to continuously improve our manufacturing processes and minimize human interference, ensuring consistent quality and performance across each batch. We achieve this through rigorous quality control measures and ongoing training for our experienced production workers.
At Honsen Magnetics, we strive to provide a seamless one-stop service, from initial design to sample production and final batch order delivery. By combining our technical expertise with a commitment to consistency, we aim to deliver high-quality precast concrete formwork magnets that meet the unique needs of our customers.
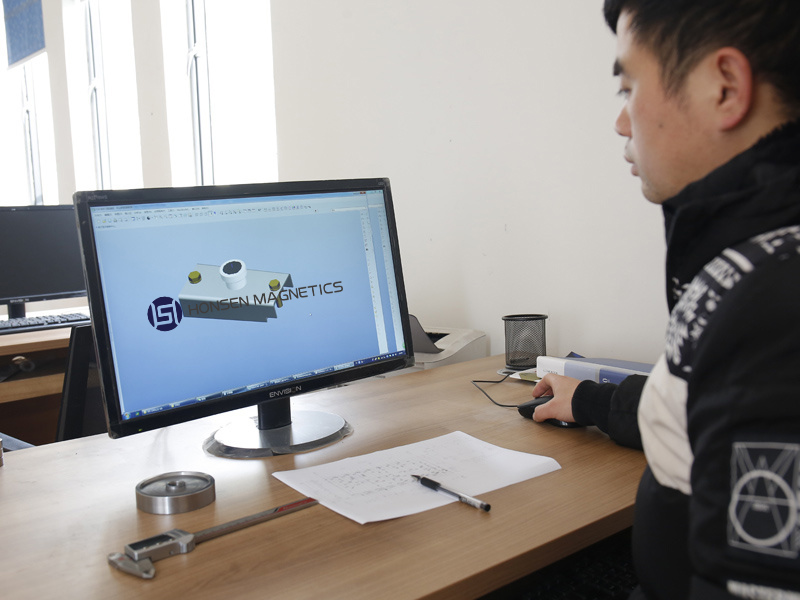
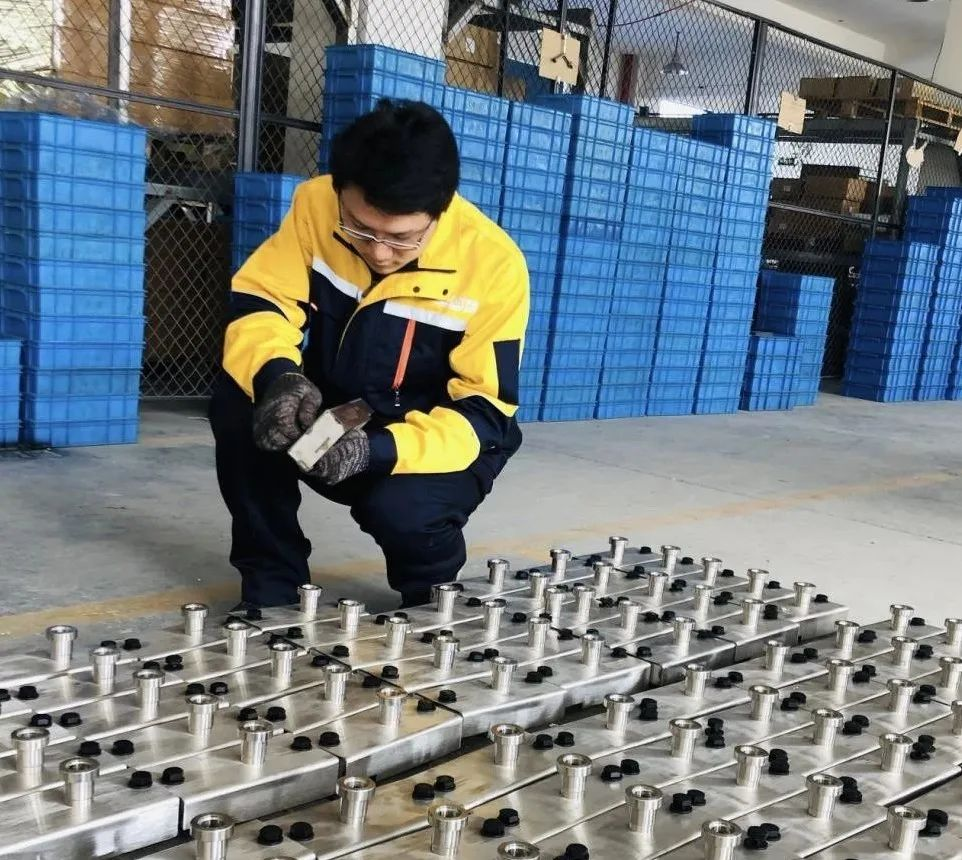
Our advantages in manufacturing Precast Concrete Formwork Magnets:
- Mechanical engineers are essential in the team, and the mechanical properties, dimensional tolerances, and other aspects of magnetic components are designed and reviewed by them. They will also develop the most reasonable processing plan based on the resources of the machining plant.
- Pursuing product consistency. There are various types of magnetic components and complex processes, such as the gluing and welding process. Manual gluing can vary from person to person, and the amount of glue cannot be controlled. The automatic dispensing machines on the market cannot adapt to our products. Therefore, we have designed and produced a dispensing system for automatic control to eliminate human factors.
- Skilled workers and continuous improvement! The assembly of magnetic components requires skilled assembly workers. We have designed and manufactured many unique and exquisite fixtures to reduce labor intensity, improve efficiency, and further ensure product consistency.
How did we do?

Listening to customer needs

Computational Design Model
In order to fully comprehend the customer's objectives, we not only focus on the key performance indicators of magnetic products but also take into account the product's operating environment, usage methods, and transportation conditions. This enables us to gather the most comprehensive information necessary for the subsequent design sampling phase. By considering all these factors, we ensure that our designs are tailored to meet the specific requirements and challenges of each customer. This holistic approach allows us to deliver magnetic products that excel in performance, durability, and practicality.
We offer comprehensive assistance in calculating and designing magnetic circuits to meet the specific needs of our customers. In addition, we take into account the processing and assembly processes to ensure the practicality of the design. Drawing on our experience and calculation results, we provide valuable improvement suggestions for any existing design flaws identified. Through collaboration with the customer, we aim to reach a mutual agreement on the final design and specifications. Upon agreement, we proceed to sign a sample order as a testament to our commitment to delivering high-quality magnetic products.
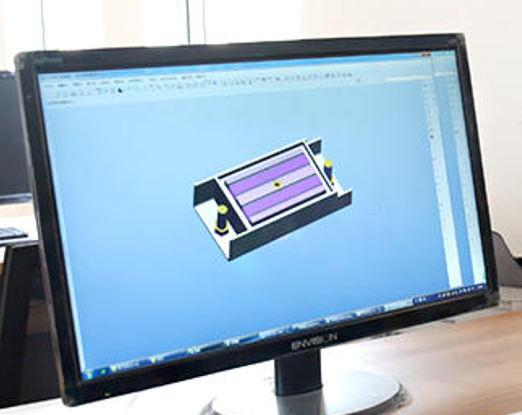
After leveraging our expertise and employing CAE-assisted calculations, we have successfully derived the ideal model. Our focus in this model revolves around two key factors: reducing the number of magnets and ensuring their ease of machining. Building on this foundation, our engineers comprehensively evaluate the design structure to simplify processing and assembly procedures. We consolidate our thoughts and effectively communicate them with our customers, striving for alignment. Once agreement is reached, we proceed to finalize the design specifications and sign sample orders with the utmost confidence in our product's performance and quality.

Develop processes and samples

Batch production control
Develop detailed processes and increase quality monitoring points. The product breakdown diagram of the magnetic device has started production.
The samples will be delivered to our customer for approval and after the confirmation of the samples, we'll start to process of bulk production.
After receiving bulk orders, arrange workers to operate, and reasonably arrange workstations and processes. If necessary, design unique tooling for processing to reduce labor intensity and ensure consistency in batch production. We have extensive experience in production control, and we need to achieve quantifiable control in all processes to ensure consistency in each batch of products.
Production Process of Magnetic Shuttering Systems
The U-shaped concrete formwork system is manufactured using iron plates with the help of a unique folding machine. The folding mechanism is responsible for creating the option of double-groove chamfer, single-groove chamfer, or no chamfer. We also use hand soldering equipment to solder formwork magnets in sizes between 2-3 m. Our production facilities are capable of producing template magnets with a height exceeding 100mm.
Template Materials
We employ during production to ensure the longevity of the magnetic formwork systems you purchase from us. We use a combination of aluminum alloy and stainless steel for their superior durability and ability to withstand extreme temperatures and wear. Except that, we employ special treatments to protect our systems from rust and corrosion. These systems are very easy to maintain because we have preprocessed them.

QUALITY & SAFETY
Quality management is the cornerstone of our company values. We firmly believe that quality is the lifeblood and compass of an enterprise. Our dedication goes beyond traditional approaches to quality management - it's woven into our operations. By utilizing this approach, we guarantee that our products consistently meet and exceed our customers' requirements, setting new benchmarks in satisfaction.
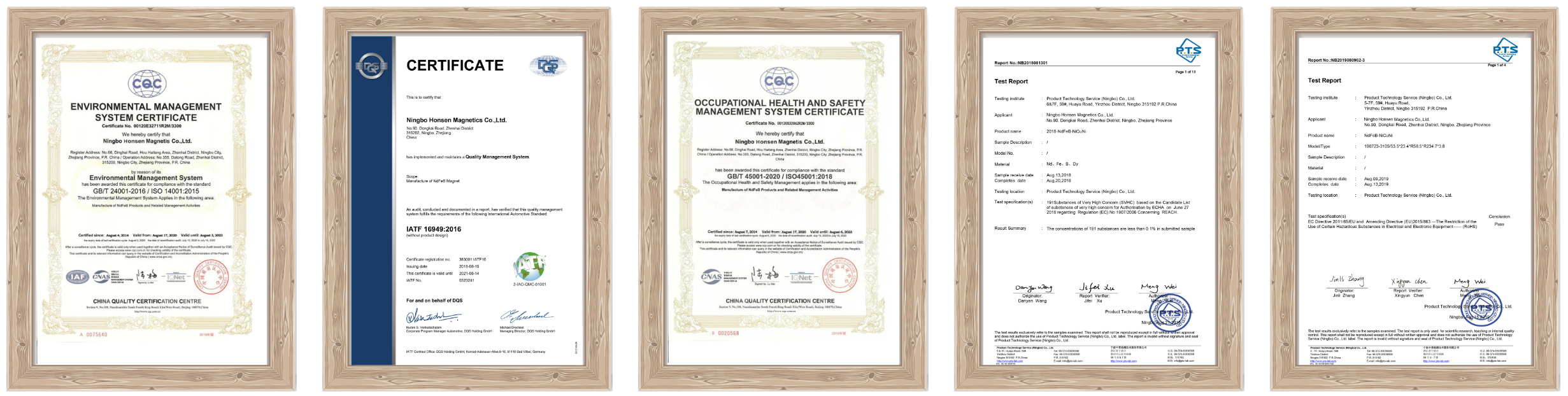
PACKING & DELIVERY

TEAM & CUSTOMERS
Our company is deeply rooted in quality management. We believe that quality is not just a concept, but the life force and guiding principle of our organization. Our approach goes beyond the surface - we seamlessly integrate our quality management system into our operations. Through this approach, we ensure that our products consistently meet and exceed our customers' expectations, reflecting our commitment to excellence.
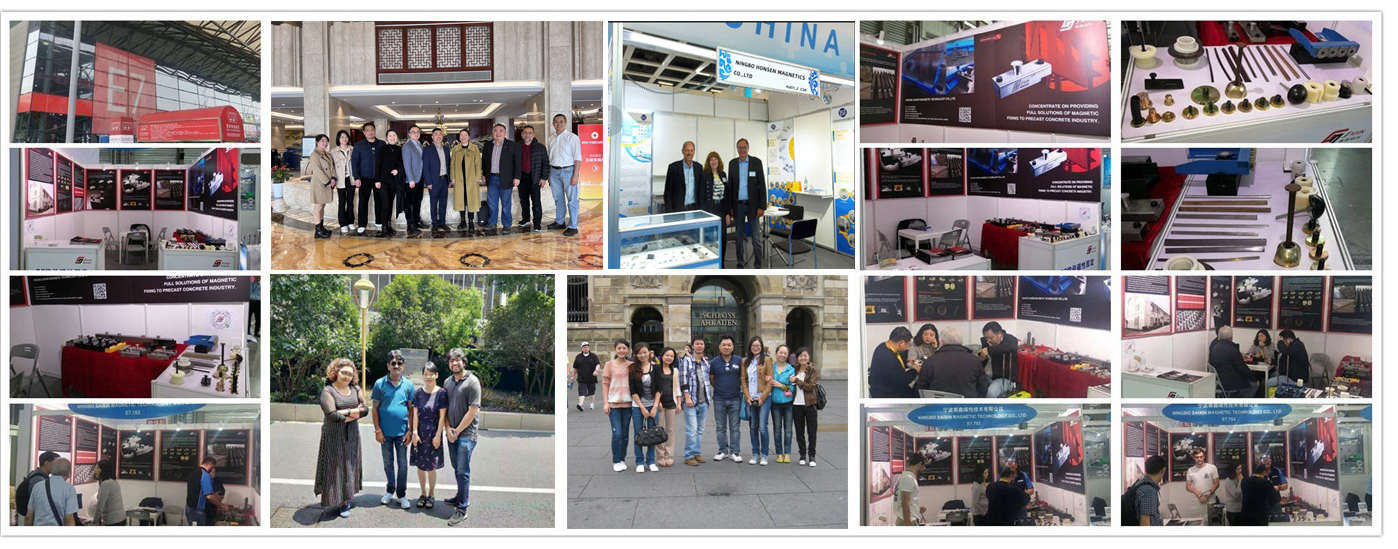
Q&A
Q: Do you accept customized projects?
A: We have optimized and designed the series dimensions, and customers can make adjustments based on this. And we also welcome our customers for any customized projects.
Q: Sample, price, and delivery time?
A: We accept sample orders. For the regular running products, we normally have samples in stock and can offer you the sample on the second day. For bulk orders, it takes 15-20 days for production.
Q: Batch quantity, price?
A: Based on the specific processing difficulty, make targeted judgments and quotations.
Q: Do you have any inventory?
A: Yes, we have regular running products in stock.
Q: What causes the diminishing holding force of shuttering magnets over time?
A: The strength of the fixed effect in shuttering magnets can weaken over time due to a few factors. One reason is the presence of foreign objects, like concrete, iron filings, or film, on the bottom surface of the magnet. When these materials accumulate, they hinder the magnet's ability to securely attach to the platform, resulting in a reduced holding force. Additionally, misalignment of the magnet can also contribute to the weakening effect. When not properly aligned, the magnet cannot establish a strong connection, leading to a decrease in its overall effectiveness. It's essential to address these issues promptly to maintain the desired holding force and prevent further weakening of the magnet over time.
Q: How can I prevent damage to my magnet?
A: To maintain the integrity of your magnet and prevent damage, consider the following measures:
- Handle with care: Treat your magnet gently and avoid dropping, banging, or subjecting it to excessive force or impact. Remember that magnets contain delicate materials that can become damaged if mishandled
- Avoid magnet-to-magnet interaction: Don't allow magnets to come into contact with each other, as they can easily chip, crack, or shatter. Keep them separated or use non-magnetic materials as barriers when storing or transporting them.
- Protect from extreme temperatures: High temperatures can affect the performance and demagnetize magnets, while very low temperatures can make them more brittle and susceptible to breakage. Keep magnets away from extreme heat sources and avoid exposing them to freezing temperatures.
- Clean carefully: When cleaning your magnet, use a soft cloth or brush to remove any dirt or debris gently. Avoid using abrasive materials or harsh chemicals, as they can scratch or corrode the magnet's surface.
- Store properly: Shield your magnet from magnetic fields by storing it in a non-magnetic container or packaging. This prevents unintentional attraction to other objects and minimizes the risk of damage.
Q: Is it normal for magnets to experience a decrease in strength over time?
A: It is common for magnets to experience a decrease in strength over time. While all magnets will lose some tension over time, Honsen Magnetics uses high-quality magnets, which have a low loss rate of only 1% within the first 10 years of use. This means that our magnets maintain their strength and performance for an extended period compared to other magnets.