Bonded Neodymium magnets are made of the powerful Nd-Fe-B material mixed into an epoxy binder. The mix is approximately 97 vol% magnet material to 3 vol% epoxy. The manufacturing process involves combining Nd-Fe-B powder with an epoxy binder and compressing the mixture in a press and curing the part in an oven. Since the material is formed by compression bonding, the dimensions typically vary .002″ or better for a given run.The Bonded Compression Molded NdFeB Magnets are widely used for simple mold and high magnetic properties, stable working temperature, good corrosion-resistance. They are possible to insert mold with other parts.
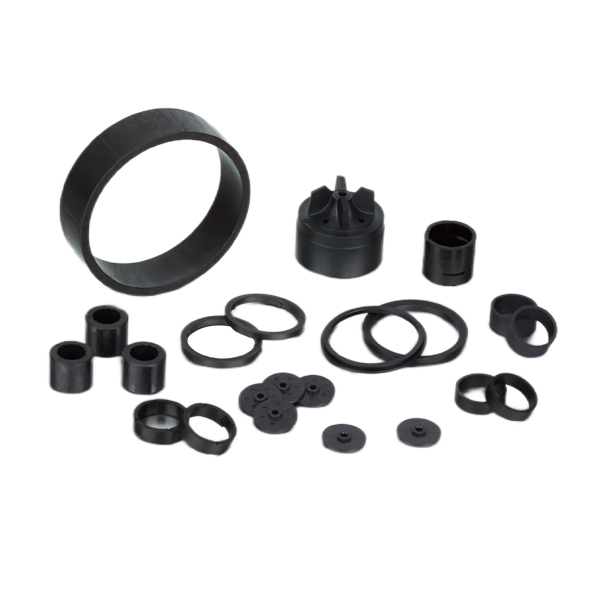
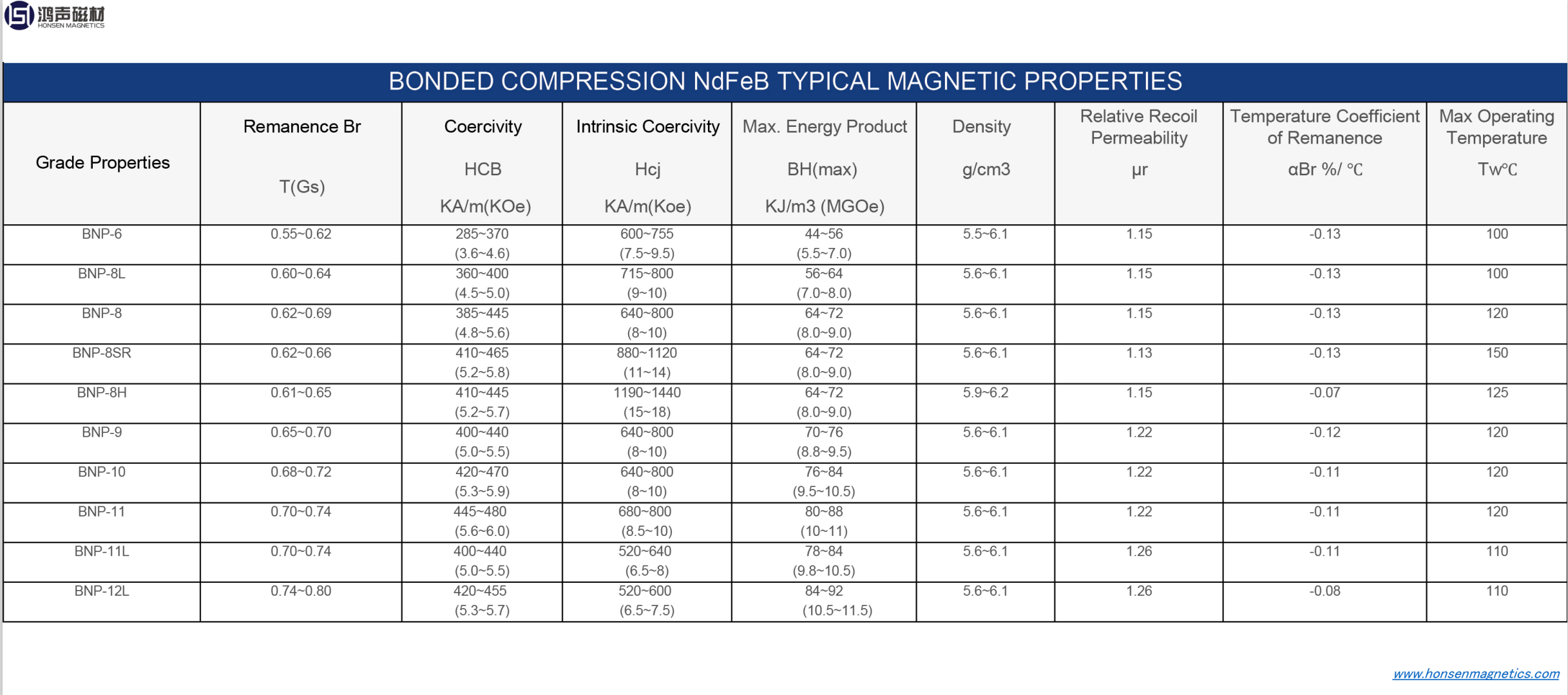
The complete combination of injecting process and high-property rare-earth powder makes it possible to form an easily strong bonded Ndfeb ring magnet for the speaker. Bonded Neodymium Magnets have the advantage of more advanced shapes compared to Sintered Magnets. The magnet needs to be coated with a layer of black or grey epoxy or Parylene to protect them against corrosion.
The Hot-pressed NdFeB magnets divided into two types, Hot pressed isotropic NdFeB (MQ 2) and hot-extruded anisotropic NdFeb magnet(MQ 3) .The Hot-pressed isotropic NdFeb magnet is produced by rapid quenched NdFeB magnetic pw der under high temperature through compression.The hot-pressed anisotropic NdFeB magnet is mainly anisotropic radially-oriented ring magnet which is produced through compression and extrusion deformation by rapidly quenched NdFeB magnetic powder under high temperature.Customized Injection Bonded NdFeB Ring Magnets

Bonded neodymium-iron-boron (NdFeB) magnets are strong magnets which are used for various applications. Epoxy coating is mostly common used for bonded NdFeB magnets; electroless nickel plating is also used to prevent corrosion. Isotropic bonded NdFeB material can be magnetized in any direction, or with multiple poles.
Bonded Nd-Fe-B material is isotropic, so it can be magnetized through any direction, including multi-polar arrangements. Because the material is in an epoxy binder, it can be machined on a mill or lathe. However, the material will not support a thread, so holes cannot be tapped. Bonded Nd-Fe-B material is often used to substantially reduce the size of designs that used ceramic magnet materials. Significant size reductions can be achieved because the material is approximately three times stronger than ceramic magnet material. In addition, since the material is isotropic, it can be magnetized multi-polar, such as a N-S-N-S pattern on the outer diameter of a ring.
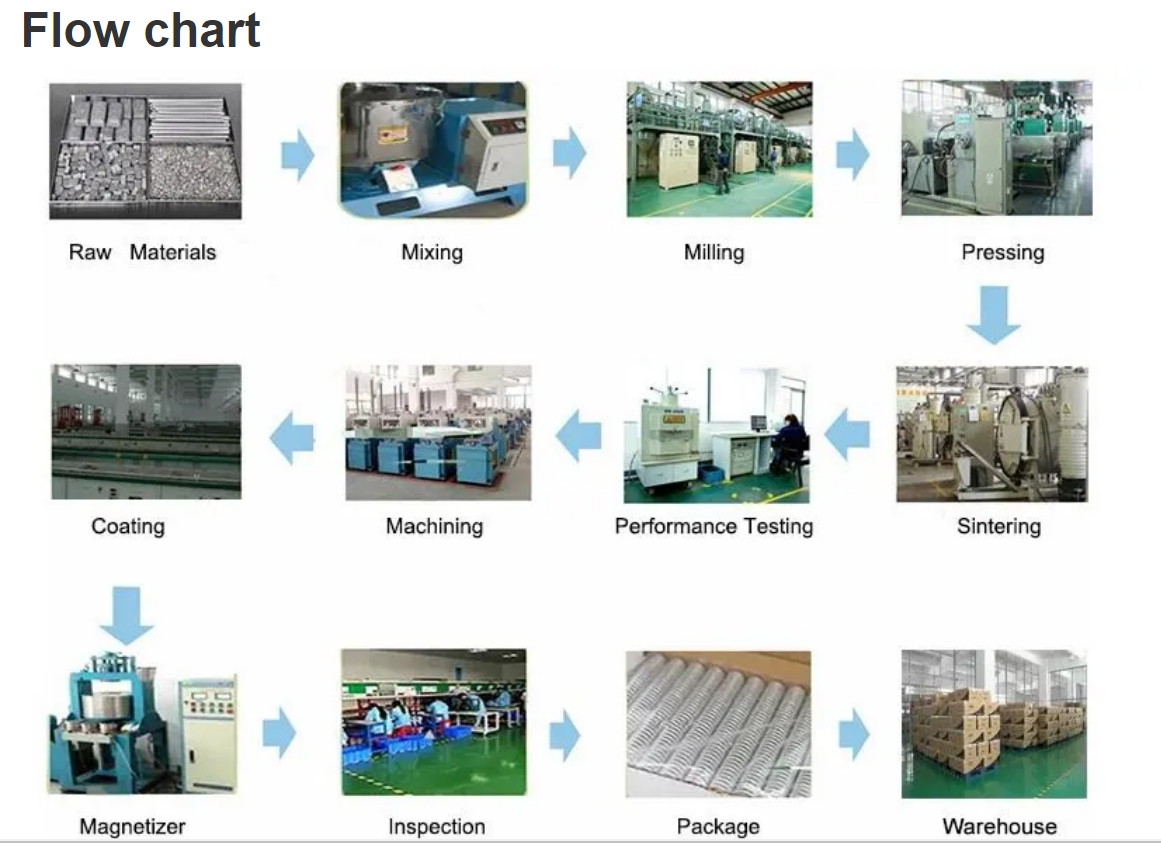
Bonded NdFeB magnets have high remanence, high coercivity, high energy product, high performance and price ratio, easy to process various sizes, and minimum specifications advantage.They can be for medina unit together with other components, widely used for short-term, small, light, and thin electronic products.
Bonded NdFeb magnets are higher magnetic strength than injection molded magnets, also have the advantage of more advanced shapes compared to sintered magnets. High coercivity, high energy product, corrosion resistance, and temperature resistance.
Bonded neodymium powder is used to create these magnets. Powder is melted and mixed with a polymer. Components are then pressed or extruded to create the product. Bonded Neodymium magnets can be magnetized into complex patterns with multiple poles. Though much weaker than Sintered Neodymium magnets, Bonded neodymium magnets give greater flexibility in terms of shapes that can be made. They are also lighter than Samarium Cobalt, and have a lower acceptable temperature (coercivity). Nevertheless, they offer excellent value for applications that require a smaller magnet or utilize radial rings.
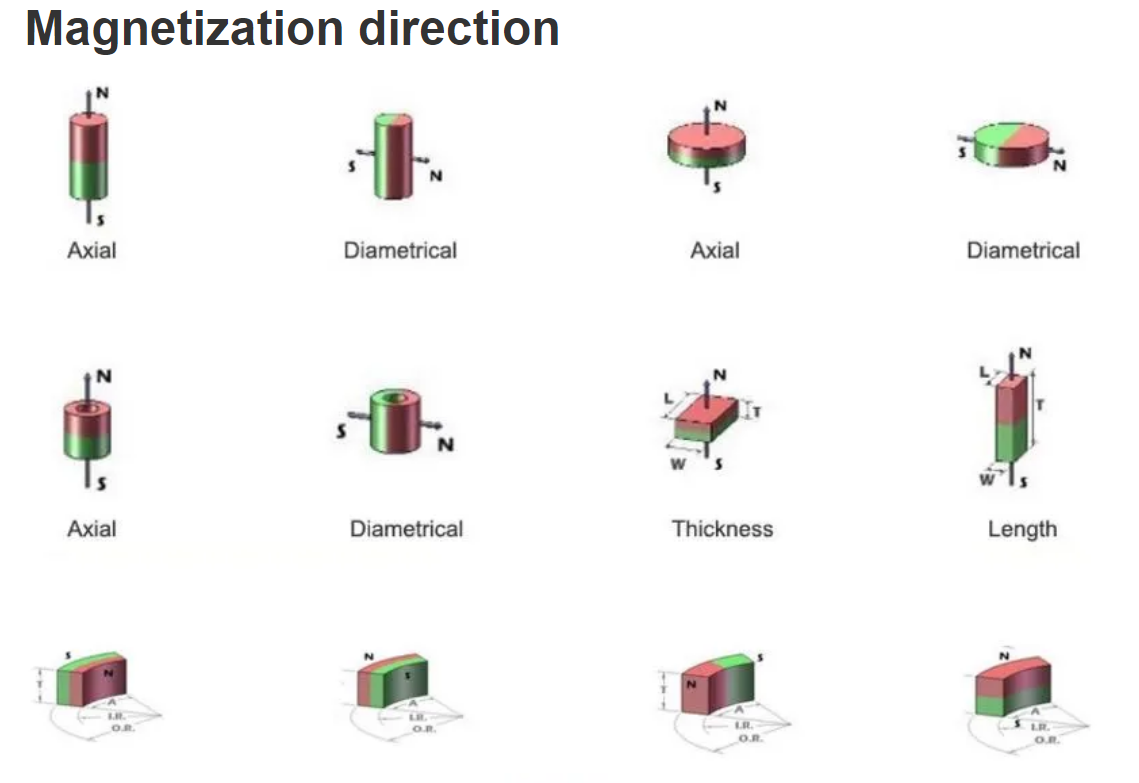
Application:
Office Automation Equipment, Electrical Machinery, Audio-visual Equipment, Instrumentation, small motors and measuring machinery, mobilephones, CD-ROM, DVD-ROM drive motors, hard disk spindle motors HDD, other micro DC motors, and automation instruments etc.
Maximum Working Temperature:
Although the Curie temperature for NdFeB material is about 310 ºC for 0% cobalt material to greater than 370 ºC for 5% cobalt, some irreversible loss of output may be expected at even moderate temperatures. Neo magnets also have a moderately high Reversible Temperature Coefficient of Induction which reduces total magnetic output as temperature rises. Selection of neo magnets instead of SmCo, is a function of the maximum temperature of the application, required magnetic output at typical working temperature and total cost of the system.
Neo magnets also have some limitations due to their corrosion behavior. In humid circumstance, a protective coating or plating is highly recommended. Coatings which have been applied successfully include; e-coating, powder coating, nickel plating, zinc plating, parylene and combinations of these coatings.
Post time: Mar-01-2023