One of the process of NdFeB magnet production: smelting. Melting is the process of producing sintered NdFeB magnets, the melting furnace produces the alloy flaking sheet, the process needs the furnace temperature to reach about 1300 degrees and lasts four hours to finish. Through this process, the raw material of the magnet is hot melted and cooled to form the alloy sheet, and the next process, hydrogen crushing, is carried out. The smelting section is carried out after the batching process, which is responsible for the casting of flakes or ingots from the batching material, both of which are done by the large and small furnaces respectively.
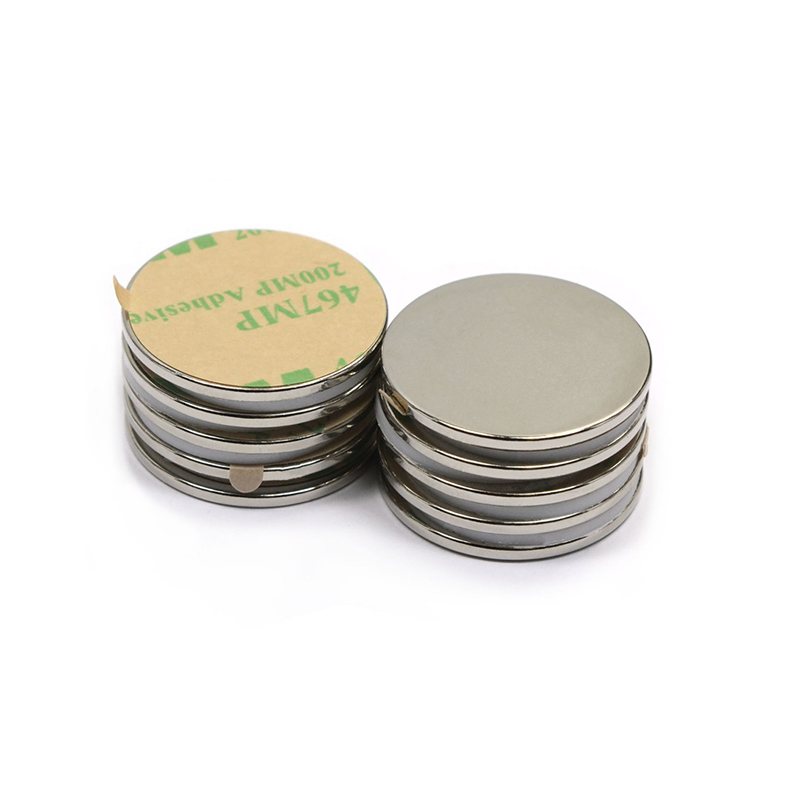
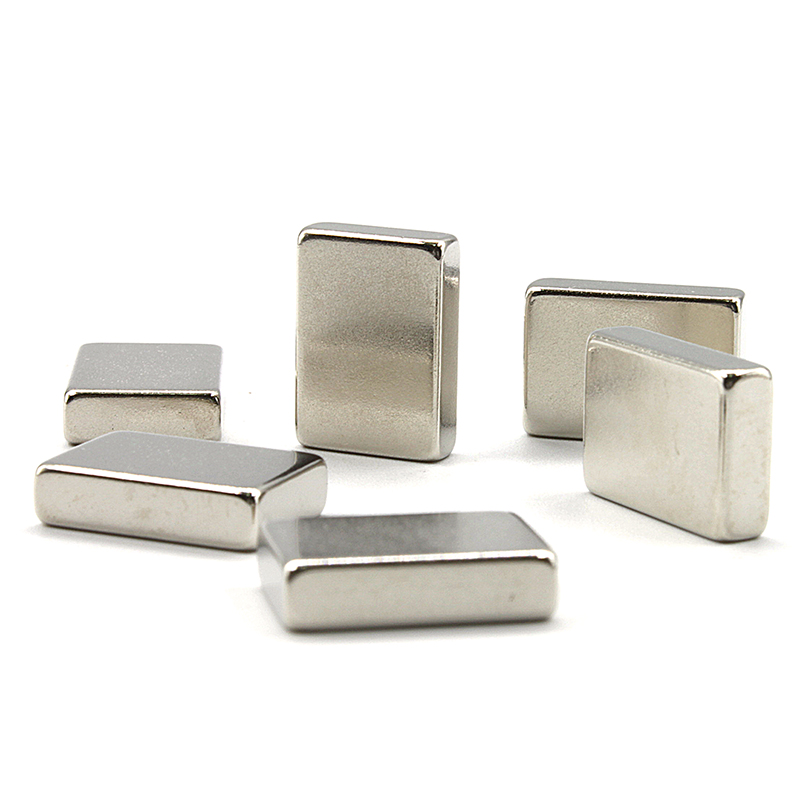
In the melting process of NdFeB magnet production, the instruments and auxiliary materials needed are basically the same, such as gloves, masks, lighting, etc. In comparison, the process of casting ingots is messy, and it is necessary to pay attention to the dressing to avoid burns when casting; secondly, when lifting, it is necessary to check the wire rope and other equipment carefully, and it is necessary to carry out in the unmanned area; thirdly, when pouring, it is necessary to pay attention to the abnormal phenomenon, and it is only when there is no abnormality that it can be continued; fourthly, it is necessary to wear a mask when replacing the middle package, to reduce the damage of dust to human body, to avoid the pollution of human body to the casting piece, and to avoid the scratch of the casting piece to human body.
The melting section of NdFeB magnet plays a crucial role in the subsequent powder making, magnetic field orientation and sintering, so if the link is not handled properly, it will have an unsalvageable impact on the overall function of the magnetic material. The magnet blanks are put into the warehouse after the magnetic function test and determined to be qualified. According to the order demand, it is discharged into the cylindrical grinding workshop. One of the NdFeB magnet production process: melting. Square NdFeB magnet billets are commonly processed by grinding: flat grinding, two end face grinding, internal round grinding, external round grinding, etc. Cylindrical NdFeB magnet blanks are often polished with no core, and double-end flat grinding. For tile magnets, fan shaped and shaped NdFeB magnets, multi-station grinder is used. After the cylindrical grinding process, all the pillars will be processed into the next process, which is the gluing of the magnet pillars, in order to prepare for the batch slicing process.
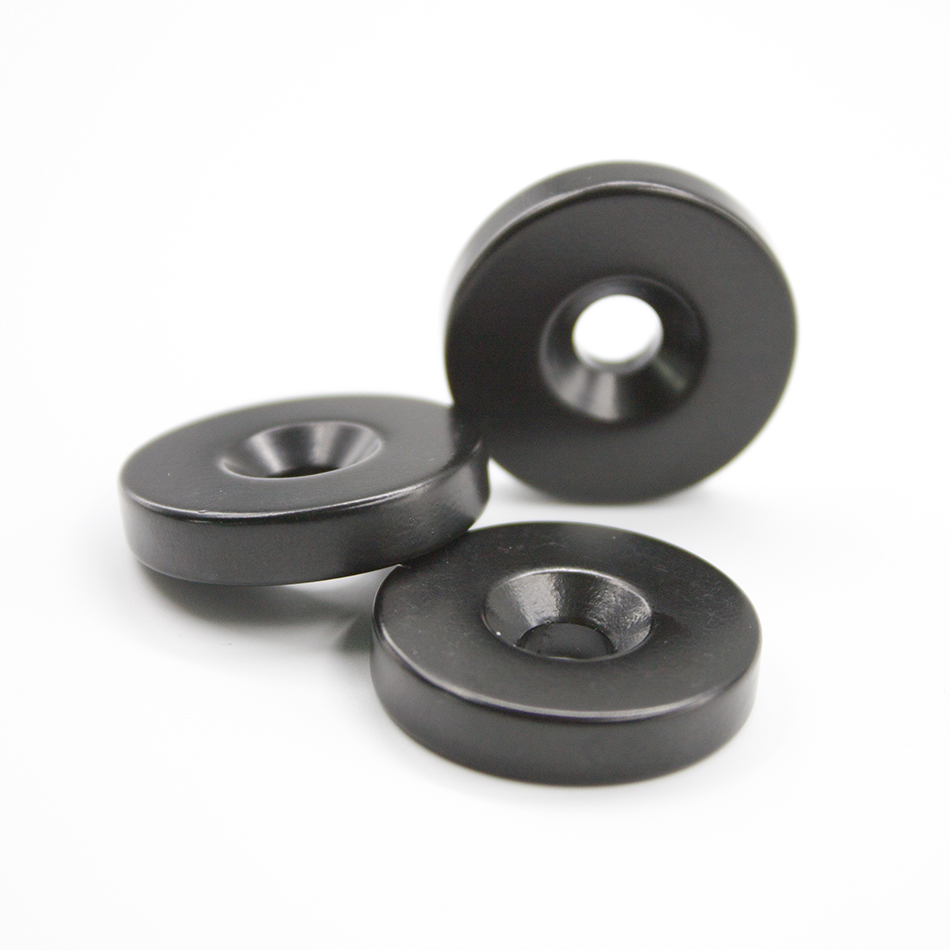
To determine whether the magnet product is qualified, not only the function is required to be qualified, but also the magnet scale metric value control directly affects its product function and application. The accuracy of the magnet scale metric value is also directly dependent on the manufacturing strength of the factory. The processing equipment is constantly updated with the economic and social market demand, and the trend of more efficient equipment and automation of industrial processing not only satisfies the increasing demand of customers for magnet precision, but also saves manpower and cost. One of the NdFeB magnet production process: melting is the competitiveness of the product with the market.
The above is the content of "NdFeB magnet production process: melting", if you still want to know more related knowledge or information, then please continue to pay attention to us. We hope you can give us your valuable comments or suggestions!
Post time: Mar-17-2022