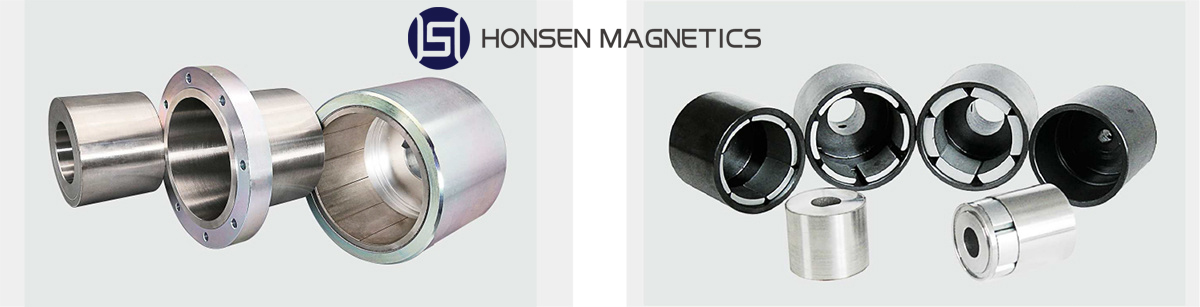
What is Magnetic Coupling?
Magnetic Coupling is a new type of coupling that connects the prime mover and the working machine through the magnetic force of the permanent magnet. Magnetic Coupling does not require direct mechanical connection, but utilizes the interaction between rare earth permanent magnets, utilizing the magnetic field to penetrate a certain spatial distance and the characteristics of material materials to transmit mechanical energy.
The magnetic coupling mainly consists of an outer rotor, an inner rotor, and a sealing can (isolation sleeve). The two rotors are separated by an isolation cover in the middle, with the inner magnet connected to the driven component and the outer magnet connected to the power component.
The magnetic couplings can be customized. The permanent magnets generally use SmCo or NdFeB magnets, and the specific grade needs to be determined based on the working temperature, working environment, and coupling torque. The shell is generally made of stainless steel (Q235A, 304/316L).
The magnetic couplings can be applied to various types of pumps and mixers such as screw pumps, gear pumps, etc. The magnetic couplings can be used to achieve sealless pumps to prevent damage caused by corrosive liquid media passing through shaft seals. Magnetic Couplings can also be applied to electric submersible equipment, such as submersible pumps, as well as various vacuum technologies and deep-sea oil drilling rigs.
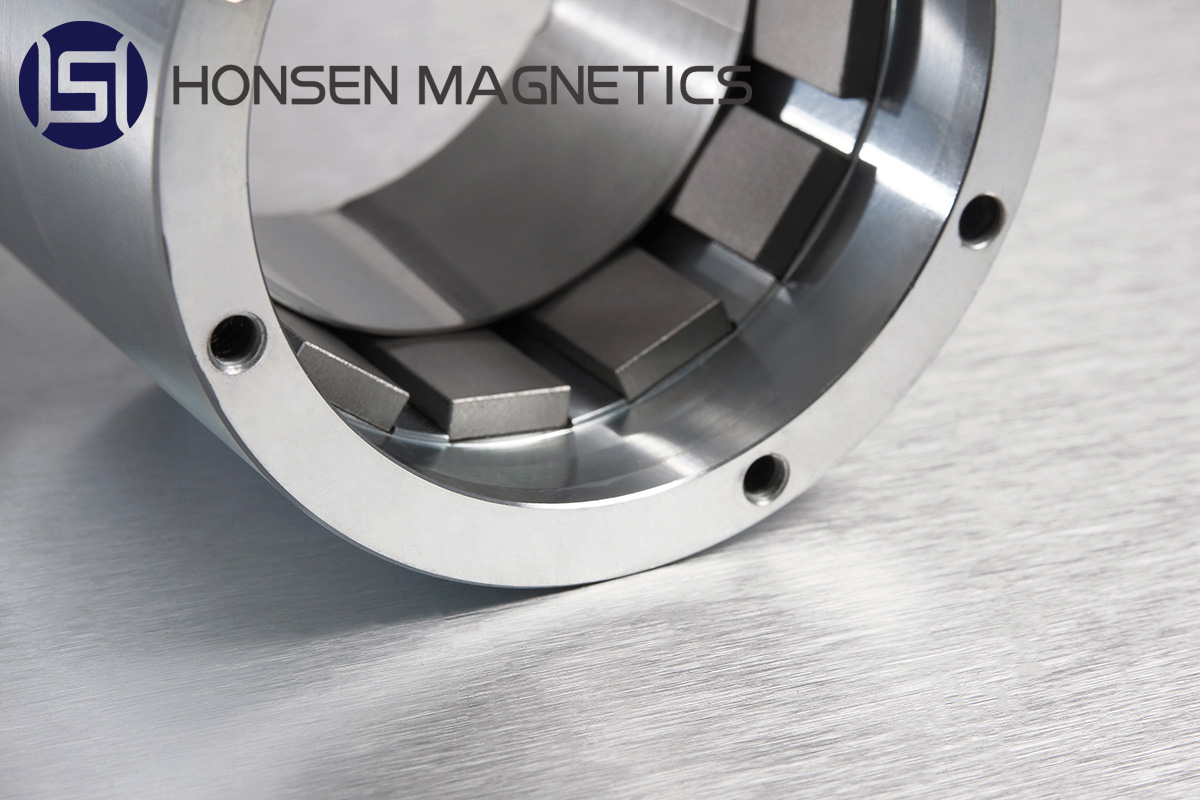
Classification of Magnetic Couplings
- Classified into magnetic transmission, it is divided into synchronous transmission (planar and coaxial), eddy current transmission, and hysteresis transmission;
- Classified into linear motion, rotational motion, and composite motion based on the mode of transmission motion;
- Classified into different structures, it can be divided into cylindrical magnetic couplings and flat disk magnetic couplings;
- Classified into different working principles, it can be divided into synchronous magnetic coupling and asynchronous magnetic coupling.
- Classified into the layout of permanent magnets, they are classified into gap dispersed type and combined pull push type.
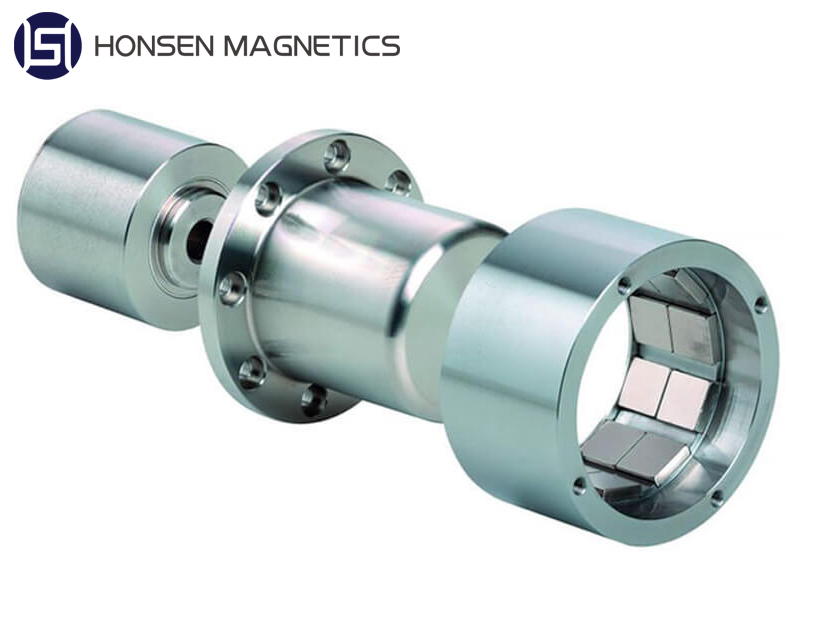
What are the main technical parameters of Magnetic Coupling?
When selecting magnetic couplings, it is necessary to comprehensively consider factors such as specific application scenarios, motor and load characteristics, and work requirements, and choose appropriate technical parameters and configuration schemes.
Magnetic coupling is a transmission device that utilizes magnetic field torque to transmit torque, and its main technical parameters include the following aspects:
- Maximum torque: represents the maximum torque that a magnetic coupling can output. This parameter is closely related to the application situation, and generally, it is necessary to choose the appropriate maximum torque value based on actual needs.
- Working speed: represents the maximum speed that the magnetic coupling can withstand. This parameter affects the range of use of magnetic couplings, and in general, a working speed that can meet the requirements should be selected.
- Loss power: Refers to the power absorbed by a magnetic coupling to convert magnetic energy into thermal energy or other forms of loss. The smaller the loss power, the higher the efficiency of the magnetic coupling, and products with low loss power should be selected as much as possible.
What are the performance characteristics of Magnetic Couplings?
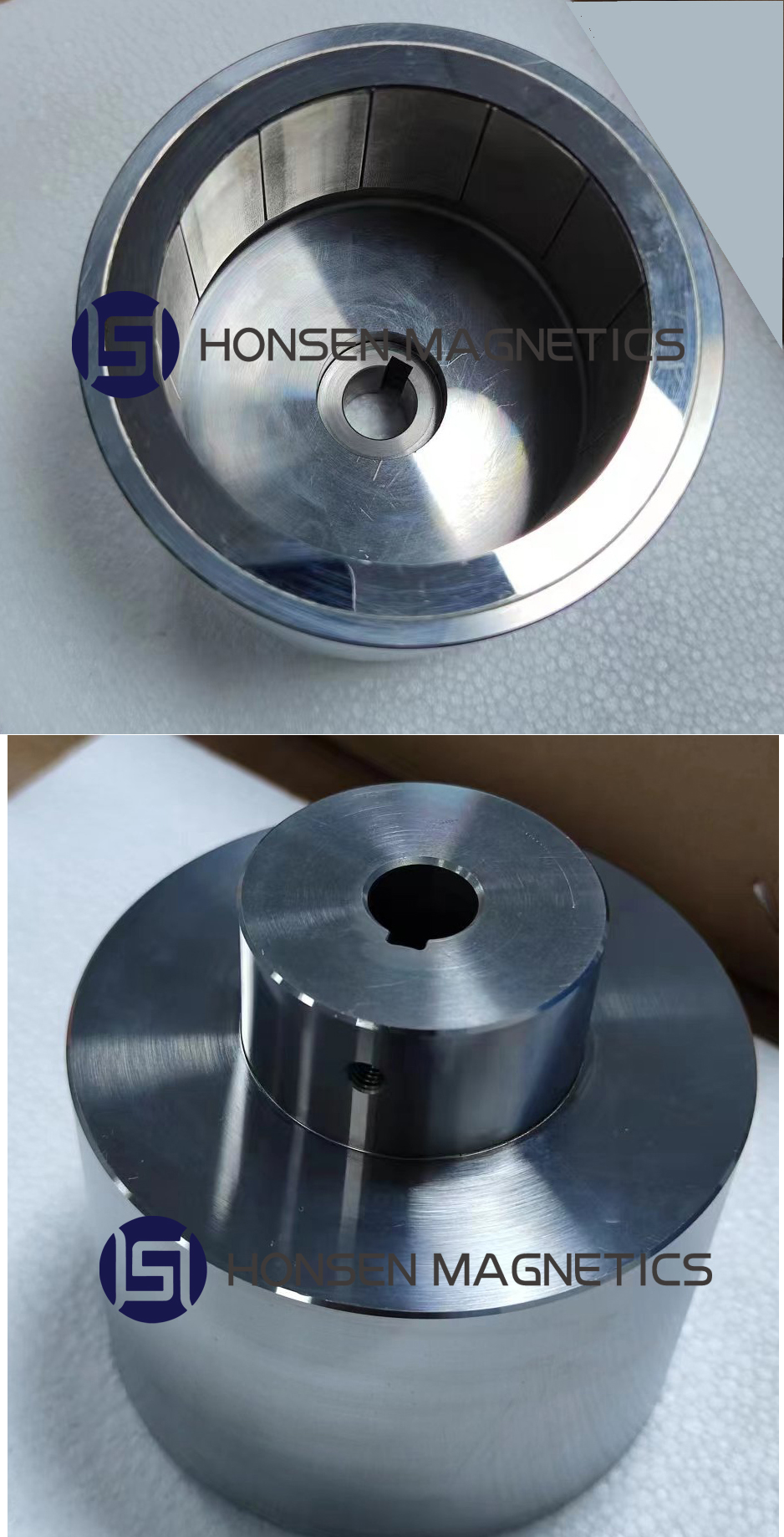
Magnet Coupling is a type of coupling based on the transmission of magnetic force through permanent magnet materials, which has the following performance characteristics:
- High transmission efficiency: Compared with traditional couplings, magnetic couplings use permanent magnet materials as magnetic media, resulting in higher transmission efficiency, reaching over 99%.
- High torque density: Due to the high magnetic energy product of permanent magnet materials, magnetic couplings of the same size can withstand greater torque compared to traditional couplings.
- Accurate torque transmission: The transmission torque of the magnetic coupling is linearly related to the input speed, so it can accurately transmit the torque that meets the requirements in practical operation and has strong adaptability.
- Strong magnetic stability: Permanent magnet materials have strong stability and magnetic field recovery. Even in high temperature and humidity environments, there will be no magnetic changes, so it has a long service life.
- Energy conservation and environmental protection: Due to the use of magnetic transmission in magnetic couplings, compared to traditional mechanical transmissions, they do not generate energy friction, heat loss, and noise pollution, thus having good energy-saving and environmental protection performance.
Why we can do Better
Honsen Magnetics specializes in the production and manufacturing of magnetic assemblies and magnetic couplings. The core team consists entirely of magnetic circuit design engineers and mechanical design engineers. After years of market integration, we have formed a mature team: from design, and sampling to batch delivery, we have tooling and fixtures equipment that can cope with mass production, some of which are designed and manufactured by ourselves, We have trained a group of experienced production workers.
We not only provide a ONE-STOP-SERVICE of design sample batch order delivery but also strive for consistency in batch products. We aim to continuously improve and minimize human interference as much as possible.
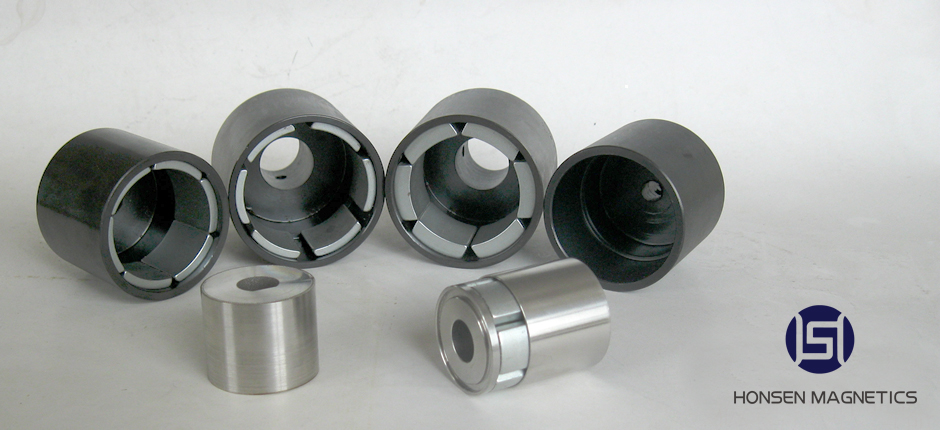
Our advantages in manufacturing Magnet Couplings:
- Familiar with various types of magnets, able to calculate and optimize magnetic circuits. We can quantitatively calculate the magnetic circuit. For example, when a customer specifies the torque of a permanent magnet coupling, we can provide the optimal and lowest-cost solution based on the calculation results.
- Experienced Mechanical engineers, the mechanical properties, dimensional tolerances, and other aspects of magnetic assemblies are designed and reviewed by them. They will also develop the most reasonable processing plan based on the resources of the machining plant.
- Pursuing product consistency. There are various types of magnetic components and complex processes, such as the gluing process. Manual gluing can vary from person to person, and the amount of glue cannot be controlled. The automatic dispensing machines on the market cannot adapt to our products. We have designed and produced a dispensing system for automatic control to eliminate human factors.
- Skilled workers and continuous innovation! The assembly of magnetic couplings and magnetic assemblies requires skilled assembly workers. We have designed and manufactured many unique and exquisite fixtures and toolings to reduce labor intensity, improve efficiency, and further ensure product consistency.
Our Facilities
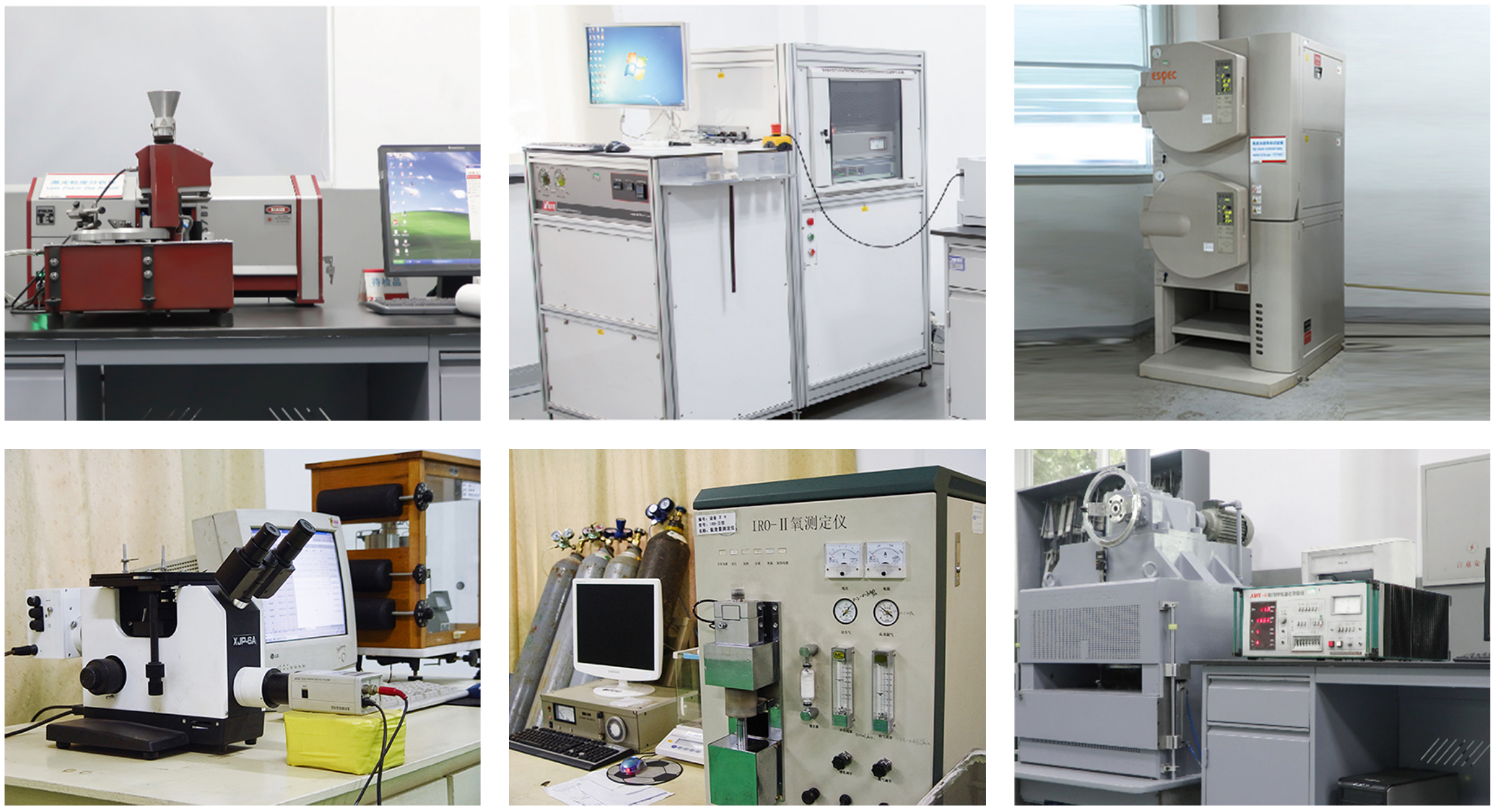
How we achieve it

Listening to customer needs
In order to fully comprehend the customer's objectives, we will take into account not only the key performance indicators of magnetic assemblies but also factors such as the operating environment, usage methods, and transportation conditions of the product. By obtaining a comprehensive understanding of these aspects, we can effectively prepare for the next phase of design sampling. This comprehensive approach ensures that our design aligns perfectly with the customer's requirements and guarantees optimal performance in real-world conditions.

Computational Design Model
Assist in calculating and designing magnetic circuits based on customer needs. Preliminary consideration of processing and assembly processes, and based on our experience and calculation results, propose improvement suggestions for the customer's imperfect design. Finally, reach an agreement with the customer and sign a sample order.
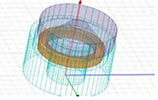
Firstly, based on our experience and CAE-assisted calculation, the optimal model is obtained. The key points of the model are that the amount of magnets should be minimized and the shape of the magnet should be easy to machine. On this basis, engineers comprehensively consider the model structure to make it easy to process and assemble. Organize our opinions and communicate with customers, and finally sign sample orders.

Develop processes and samples
Develop detailed processes and increase quality monitoring points. The product breakdown diagram of the magnetic device has started production.
Design fixtures: 1. Ensure the shape, position, and dimensional tolerances of the parts; 2. Used for measuring equipment to ensure quality.
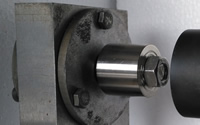
This is an example of our designed exclusive testing facility. After signing the sample order, based on the processing and assembly characteristics, we need to develop detailed processes and increase quality monitoring in key processes. At the same time, we produce tooling fixtures. At this stage, the tooling is used to ensure the geometric and dimensional tolerances of the parts and the entire product, and for parameter testing to ensure that our products can be quickly and efficiently inspected in subsequent batches.

Bulk production control
After receiving bulk orders, arrange workers to operate, reasonably arrange workstations and processes, and if necessary, design unique tooling for processing to reduce labor intensity and ensure consistency in batch production.
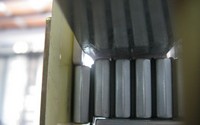
Magnet dismantling equipment
Permanent magnet couplings, motor magnets, and some magnetic assemblies require magnets to be magnetized before assembly. Manual disassembly of magnets is inefficient, and the most important thing is that it is painful to peel off the magnets with your fingers for a long time. Therefore, we have designed and manufactured this small equipment to completely relieve worker pain and improve efficiency.
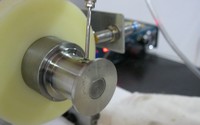
Automatic gluing equipment
Many magnetic couplings and components require the use of glue to bond strong magnets and other components together. Unlike manual gluing, the amount of glue cannot be controlled. We have designed and manufactured automatic gluing equipment specifically for our products, which is more efficient and efficient compared to equipment sold on the market.
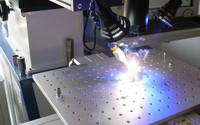
Automatic laser welding
Many of our order products require laser welding of workpieces for sealing purposes (some magnetic components require the magnet to be completely sealed). In actual welding, the workpieces have tolerances and there is thermal deformation during welding; It is not practical to manually weld large quantities of orders. We have designed and manufactured many specialized fixtures to enable beginners to quickly get started.
We have extensive experience in production control, and we need to achieve quantifiable control in all processes to ensure consistency in each batch of products.
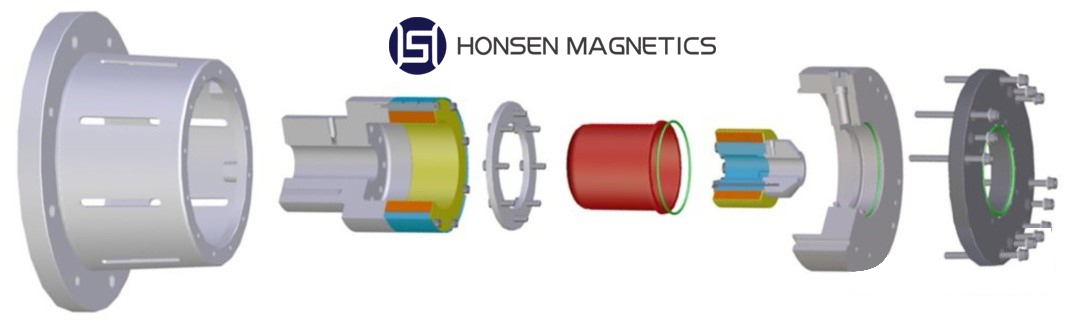
PACKING & DELIVERY

Q&A
Q: Is there any drawings?
A: We have optimized and designed the series dimensions of the coupling, and customers can make adjustments based on this. And we also welcome our customers for any customized projects.
Q: What's the sample, price, and lead time?
A: At the beginning of the magnetic coupling project, sample testing is always required, so we accept sample orders. However, in order to screen out customers with batch intentions, we will charge a higher sample fee. We will charge a sample fee ranging from 3000 to 8000 yuan for torque from 0.1 Nm to 80 Nm, and the delivery time is generally 35 to 40 days.
Q: How about the bulk MOQ and the price?
A: Based on the specific processing difficulty, make targeted judgments and quotations.
Q: Do you have any inventory?
A: Magnetic couplings are mostly customized. For example, if customers require different shaft holes, we need to rework the parts, so we do not stock the finished products. All customized production, no inventory.
Q: Will magnetic couplings lose magnetic performance?
A: Magnetic couplings use permanent magnets to transmit torque without gaps. When the permanent magnet demagnetizes or loses excitation, the magnetic coupling becomes ineffective. The main demagnetization methods of permanent magnets include high temperature, vibration, reverse magnetic field, etc. Therefore, our magnetic coupling must operate in a synchronous state of the inner and outer rotors. When the load is too large, the outer rotor repeatedly loads the reverse magnetic field on the inner rotor, which is easily demagnetized, leading to torque reduction or complete failure.
Q: What should I pay attention to when installing a magnetic coupling?
A: The magnetic coupling is a non-contact transmission, with a certain gap between the outer rotor and the isolation sleeve, as well as between the isolation sleeve and the inner rotor, greatly reducing the difficulty of installation. However, the wall thickness of the isolation sleeve is very thin, and if it collides with other components or hard particles during operation, it will damage the isolation sleeve and fail to function as a seal. Therefore, it is necessary to ensure a certain degree of coaxiality according to different clearances.
Q: How to choose a model?
A: Firstly, determine the torque of the small coupling based on the rated power and rated speed of the motor. The rough calculation formula is coupling torque (Nm)=10000 * motor power (kW)/motor speed (RPM); Secondly, it is necessary to understand the working temperature, working pressure, and medium anti-corrosion. Our magnetic coupling requires a speed of less than 3000RPM and a working pressure of less than 2MPa.
Q: How does a permanent magnet coupling work?
A: Magnet Couplings are also available in various structural forms. Our permanent magnet couplings use the principle of strong magnets attracting each other for non-contact transmission. Composed of inner and outer rotors, assembled with super-strong magnets. The motor drives the outer rotor to rotate while transferring kinetic energy to the inner rotor through the magnetic circuit of the inner and outer rotors, causing the inner rotor to rotate synchronously. This type of magnetic coupling achieves static sealing due to the lack of hard connections between the internal and external transmission shafts and is widely used in transmission systems for corrosive, toxic, and polluting liquids or gases.