About Hard Ferrite (Ceramic) Magnets
Ceramic Magnets, also known as Ferrite Magnets, contain materials such as sintered iron oxide and barium or strontium carbonate. Ferrite Magnets are known for their low cost, good corrosion resistance, and high-temperature stability up to 250 ° C. Although their magnetic properties differ significantly from NdFeB magnets, their cost is very low because of the cheap, abundant, and nonstrategic raw materials used to manufacture these magnets, making permanent magnet ceramic magnets suitable for large-scale production.
Ferrite Magnets are made by molding a powder mixture of about 80% Fe2O3 and 20% either BaCo3 or SrO3. Along with further research, additives such as cobalt (Co) and lanthanum (La) are combined to improve magnetic performance. The metallic green molded powder is sintered inside a temperature-controlled furnace that is heated by electricity or coal. Though hard ferrite magnets have low magnetic properties, they are still a preferred choice for engineers due to several factors such as abundant raw material availability, the lowest cost among permanent magnet families, low density, excellent chemistry stability, high maximum working temperature, and Curie temperature.
Segment Ferrite & Ring Ferrite Magnet is the most commonly marketed product and serves as an important business pillar for our company in its early stages. With the realization of increasing demand for these applications, we have focused our efforts on the promotion of arc segment-type hard ferrite magnets and have amassed extensive experience in properly producing magnets to maximize performance and optimize other application intentions. We also succeeded in developing a hard ferrite magnet with an irregular structure, complicated geometry, and high precision. Our marketed hard ferrite magnets are now widely used inside motors, generators, sensors, loudspeakers, meters, relays, separators, and a variety of other applications in defense, automotive, robotics, household appliances, wireless communication base stations, and mineral plants.
Schematic diagram of magnetic force comparison between Ferrite Magnet and Neodymium Magnet--->
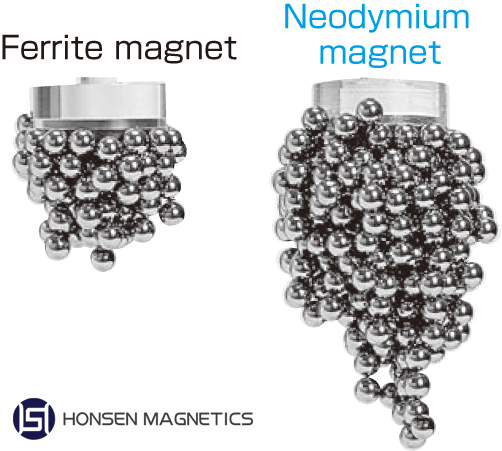
Ferrite Magnets have low energy products and good corrosion resistance and are typically used in components containing low-carbon steel, capable of operating at moderate temperatures. Making ceramic magnets requires pressing and sintering. Due to their potential brittleness, diamond grinding wheels should be used if grinding is required. Ferrite Magnets strike a balance between magnetic strength and cost-effectiveness, while their brittleness trend balances their excellent corrosion resistance. They also have strong coercivity and resistance to demagnetization, making them an economic choice for common applications such as toys, handicrafts, and motors. Rare earth magnets can greatly improve weight or size, while ferrite has become a better choice for applications with low energy density requirements, such as power windows in vehicles, seats, switches, fans, blowers in electrical appliances, some power tools, and speakers and buzzers in electroacoustic equipment.
Strontium Hard Ferrite Magnet & Barium Hard Ferrite Magnet
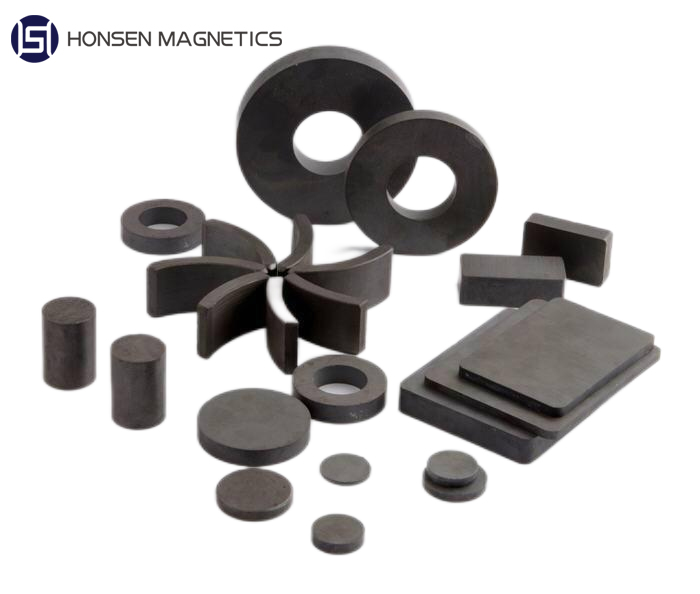
The chemical composition of barium hard ferrite magnet and strontium hard ferrite magnet is described by the formulas BaO-6Fe2O3 and SrO-6Fe2O3. Strontium hard ferrite magnet outperforms barium hard ferrite magnet in terms of magnetic performance and coercive force. Because of the lower material cost, barium hard ferrite magnets are still widely used. To achieve high magnetic properties while saving money, a mixture of strontium carbonate and barium carbonate is sometimes used to manufacture hard ferrite.
Direct contact with a barium ferrite magnet is generally considered safe, as long as it is used in accordance with proper handling procedures. However, it is important to note that barium is a toxic element, and precautions should be taken to prevent ingestion or inhalation of any barium dust or particles. It is advisable to always wash hands thoroughly after handling barium ferrite magnets and avoid activities that may generate fine particles or dust. If any concerns arise or if there is a need for specific safety information, it is recommended to consult us or relevant safety guidelines.
Shapes and Dimensional Tolerance of Hard Ferrite Magnets
Hard ferrite magnets come in various shapes and types. The most common shapes include rings, arcs, rectangles, discs, cylinders, and trapeziums. These shapes can be customized and combined to meet specific needs. Additionally, hard ferrite magnets are available in different types, such as isotropic and anisotropic. Isotropic magnets have uniform magnetic properties in all directions, while anisotropic magnets have a preferred magnetization direction. This allows for further machining based on application requirements. With their versatility in shape and type, hard ferrite magnets are widely used in industries such as automotive, electronics, and energy.
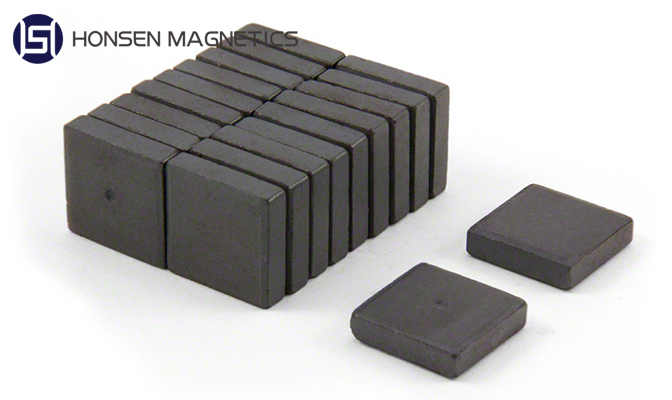
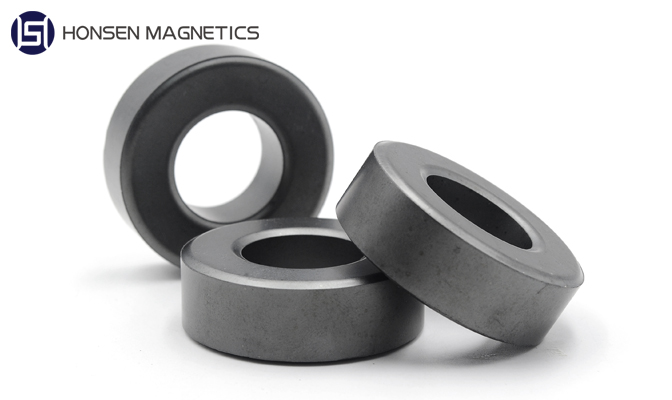
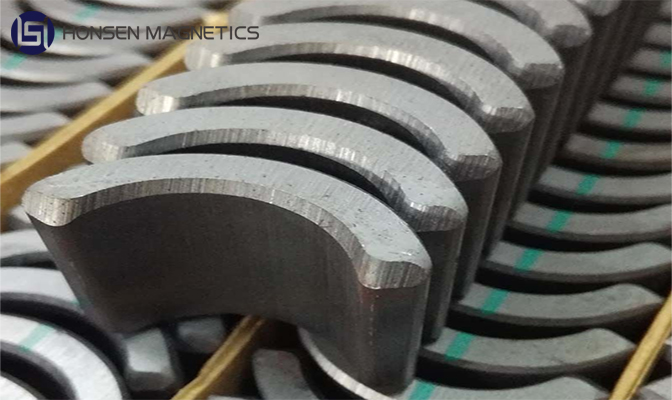
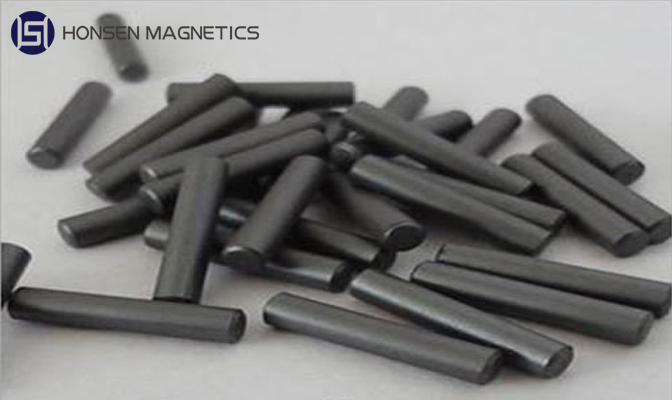
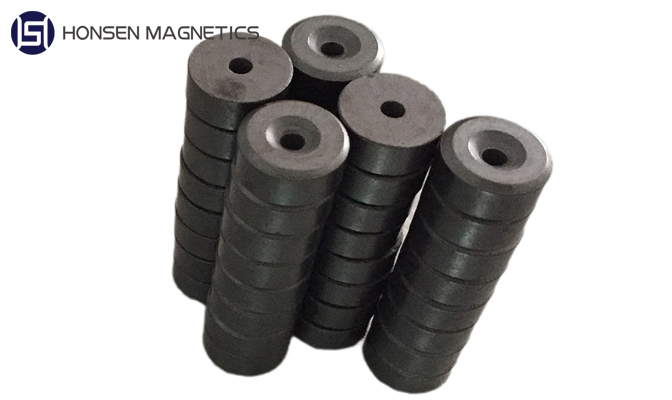
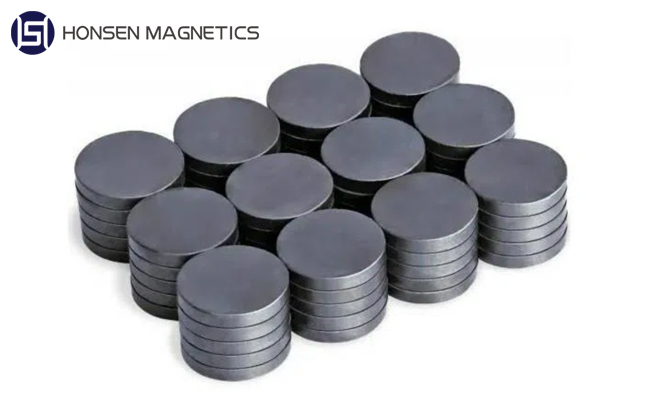
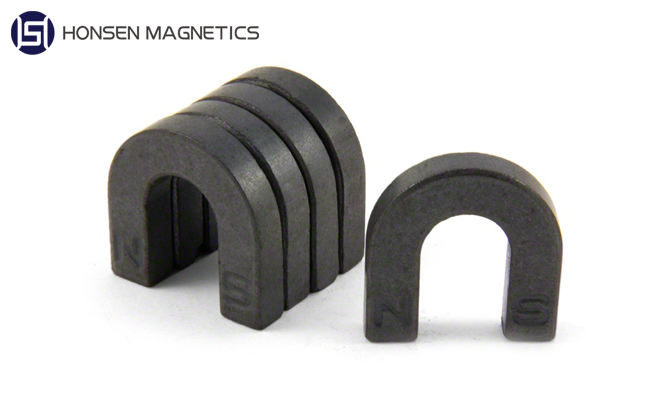
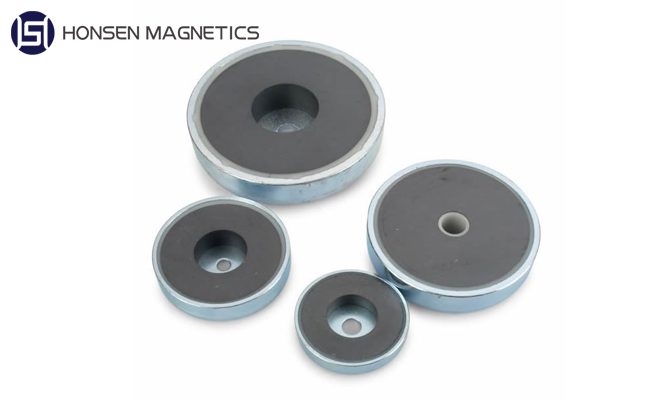
Before being machined, the dimensional deviation of a hard ferrite magnet is controlled to within +/-2%, and after being simply ground with a diamond tool, it can be controlled to within +/-0.10mm. Customs tolerance or precise control of up to +/-0.015mm is possible but must be negotiated. Wet anisotropic hard ferrite magnets are typically supplied with surfaces parallel to anisotropic orientation un-ground and other surfaces ground. For definitions of concentricity, roundness, squareness, perpendicularity, and other tolerances, please contact our team.
Manufacturing Process of Hard Ferrite Magnets
The manufacturing process of Hard Ferrite Magnets involves several steps.
1. The raw materials, including iron oxide and strontium carbonate or barium carbonate, are mixed together in a precise ratio. The mixture is then milled into a fine powder.
2. The powder is compacted into the desired shape using either a hydraulic press or an isostatic press. The compacted powder is then sintered at high temperatures, typically around 1200-1300 degrees Celsius, in a controlled atmosphere to promote grain growth and increase magnetic properties.
3. After the sintering process, the magnets are cooled slowly to room temperature to minimize stress and prevent cracks. They are then machined or ground to achieve the final desired shape and dimensions.
4. In some cases, an additional step of magnetization is required. This involves subjecting the magnets to a strong magnetic field to align the magnetic domains in a specific direction, further enhancing their magnetic properties.
5. Finally, the magnets undergo quality control checks to ensure they meet the desired specifications and requirements before being packaged and shipped to customers.
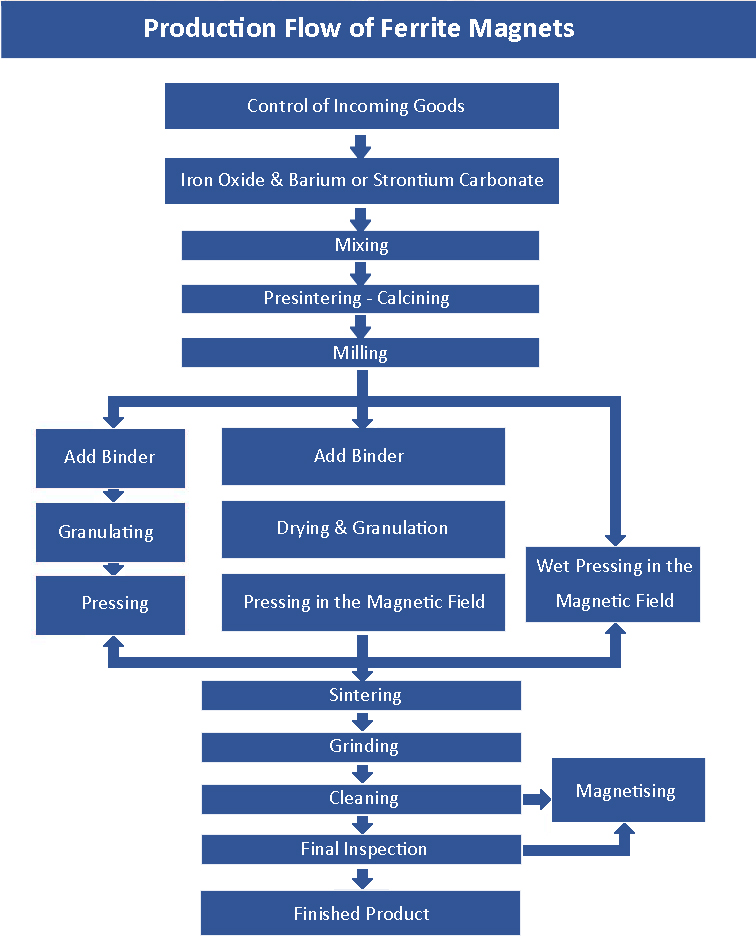
Tooling of Hard Ferrite Magnet
Molding using tooling is the most cost-effective method for producing large quantities of hard ferrite magnets. Creating anisotropic hard ferrite magnets requires expensive tooling, whereas making isotropic hard ferrite magnets is far less expensive. We can use the ready tooling to mold alternative thickness/height magnets within the range allowed if the required magnet has the same diameter as the current tooling, or the same length and width when it is a block type.
In reality, we occasionally cut large blocks, grind larger ring or disc diameters, and machine arc segments of close dimension to the needed one. When the order quantity is not very large (especially at the prototype phase), this approach is effective for obtaining precise dimensions, saving tooling costs, and homogenizing the weight and flux of each piece of the product. The cost of machine-made magnet production is very high.
Wet Anisotropic, Dry Isotropic & Anisotropic Hard Ferrite Magnet
The majority of hard ferrite magnets are molded using a press machine equipped with a coil capable of producing an external magnetic field, resulting in an anisotropic magnet. The material used to make anisotropic hard ferrite magnets is typically in a wet slurry state, allowing molecules to be perfectly aligned during the molding process. We call magnets made by this process wet anisotropic hard ferrite magnets because they can only be magnetized along a pre-orientation. The (BH)max of an anisotropic hard ferrite magnet is several orders of magnitude greater than that of an isotropic hard ferrite magnet.
The raw material used to make isotropic hard ferrite magnets is typically dry powder. The molding is done with a punch machine, which cannot apply an external magnetic field to the magnet. As a result, the magnets that result are known as dry isotropic hard ferrite magnets. Magnetization on an isotropic hard ferrite magnet could take place in any desired orientation and pattern, depending on the magnetizing yoke.
Dry anisotropic hard ferrite magnets are another type of hard ferrite magnet. It is made of dry powder that has been oriented by an external magnetic field. The magnetic property of a dry anisotropic hard ferrite magnet is lower than that of a wet anisotropic hard ferrite magnet. Typically, a dry and anisotropic process is used to mold magnets with complex structures but superior properties to isotropic magnets.
Anisotropic, Diametrically Oriented Hard Ferrite Magnet
With axial magnetization, ring-type anisotropic hard ferrite magnets are most frequently utilized (parallel to pressing orientation). There are some market needs for ring-shaped anisotropic hard ferrite magnets with diametrical magnetization (oriented perpendicular to the pressing axis), which are particularly challenging to produce. The time-rotors, sensors, stepping motors, and pump motors of household appliances, such as washing machines, dishwashers, aquariums, and heat-supply systems, are intended to utilise this type of magnet. The clash between rising magnetic force and falling product crack ratio poses a production challenge. Magnet crack will frequently occur during the sintering and shaft injection procedures. After more than ten years of research, our engineer was able to remove the bottleneck and gained some unique experience in producing this type of magnet.
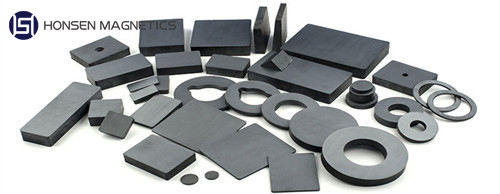
Thermal Properties of Hard Ferrite Magnet
Hard ferrite's negative temperature coefficient of remanence. Hard ferrite magnets have a positive temperature coefficient of intrinsic coercive force compared to rare earth magnets. Hard ferrite magnets' remanence will decrease as temperature rises by 0.18%/°C, whereas their intrinsic coercive force will rise by roughly 0.30%/°C. The coercive force of a hard ferrite magnet will decrease as external temperature decreases. As a result, it is advised to have components with hard ferrite magnets that do not operate at low temperatures. Hard ferrite magnets have a curie temperature of roughly 450°C. The hard ferrite magnet's recommended operating temperature range is -40°C to 250°C. Hard ferrite magnets will experience a change in grain structure when the ambient temperature reaches up to roughly 800oC. This temperature prevented the magnet from working.
Chemical Stability & Coating
Hard ferrite magnets have high chemical stability in the majority of situations. It is resistant to a wide range of substances, including brines, diluted acids, potassium and sodium hydroxides, alkaline solutions, and organic solvents. Concentrated organic and inorganic acids, including sulphuric, hydrochloric, phosphoric, hydroflouric, and oxalic acids, have the ability to etch it. Concentration, temperature, and contacting time all affect the degree and speed of etching. It does not require coating for protection because corrosion will not occur even when it operates in a humid and warm environment. It could be painted or nickel and gold plated, for example, for purposes of beauty adornment or surface cleaning.
WHY CHOOSE US
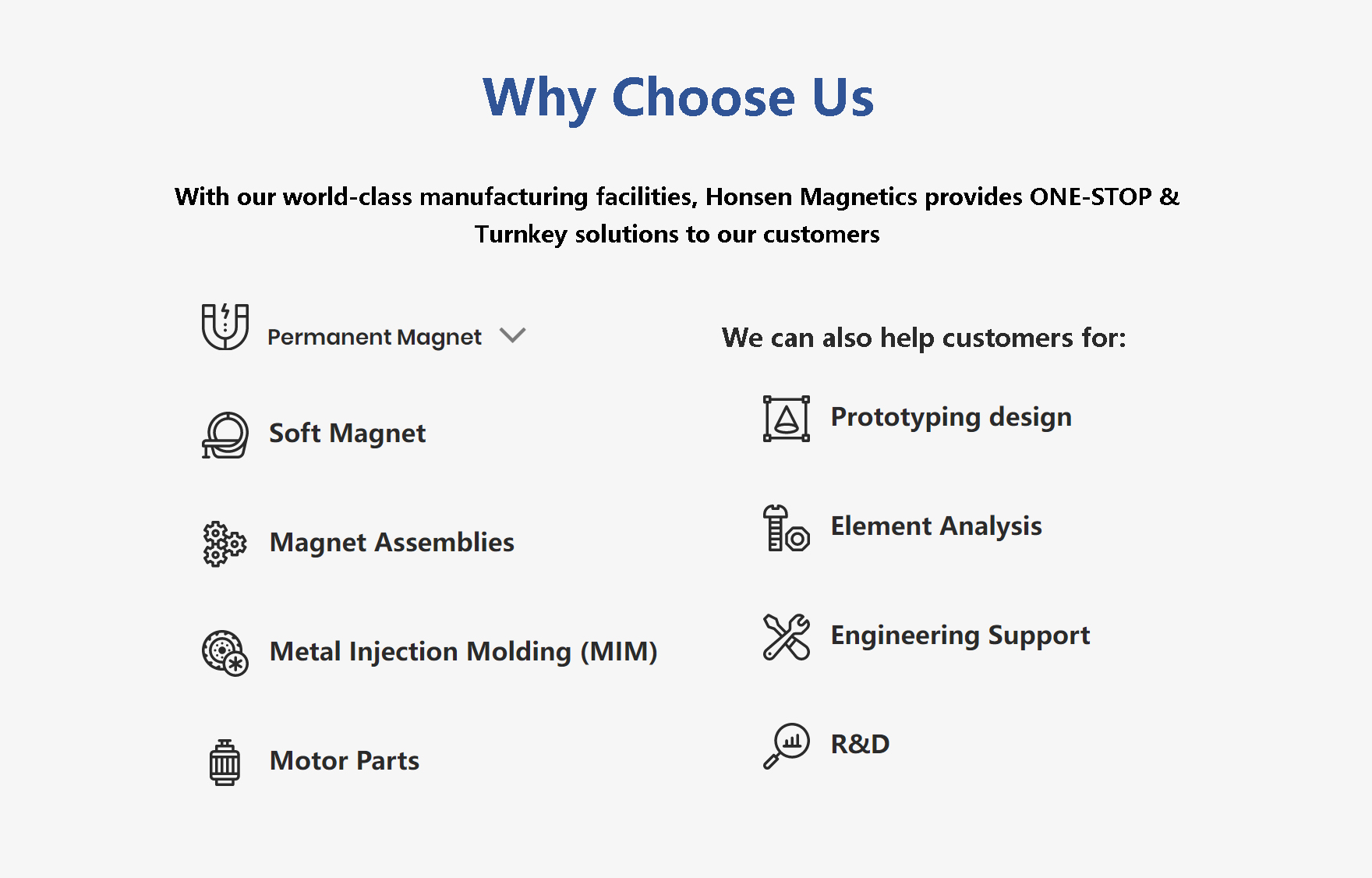
With over a decade of experience, Honsen Magnetics has consistently excelled in the manufacturing and trading of Permanent Magnets and Magnetic Assemblies. Our extensive production lines encompass various crucial processes such as machining, assembly, welding, and injection molding, which allows us to provide our customers with ONE-STOP-SOLUTION. These comprehensive capabilities allow us to produce top-notch products that meet the highest standards of quality.
At Honsen Magnetics, we take great pride in our customer-centric approach. Our philosophy revolves around putting the needs and satisfaction of our clients above everything else. This commitment ensures that we not only deliver exceptional products but also provide excellent service throughout the entire customer journey. By consistently offering reasonable prices and maintaining superior product quality, we have gained immense popularity in Europe, America, Southeast Asia, and other countries. The positive feedback and trust we receive from our customers further solidify our standing in the industry.
OUR ADVANTAGES
- More than 10 years of experience in the permanent magnetic products industry
- Have a strong R&D team can provide perfect OEM&ODM service
- Have the certificate of ISO 9001, IATF 16949, ISO14001, ISO45001, REACH, and RoHs
- Strategic cooperation with the top 3 rare blank factories for raw materials
- High rate of automation in Production & Inspection
- Pursuing product consistency
- Skilled workers & continuous improvement
- 24-hour online service with first-time response
- Serve ONE-STOP-SOLUTION ensure efficient & cost-effective purchasing
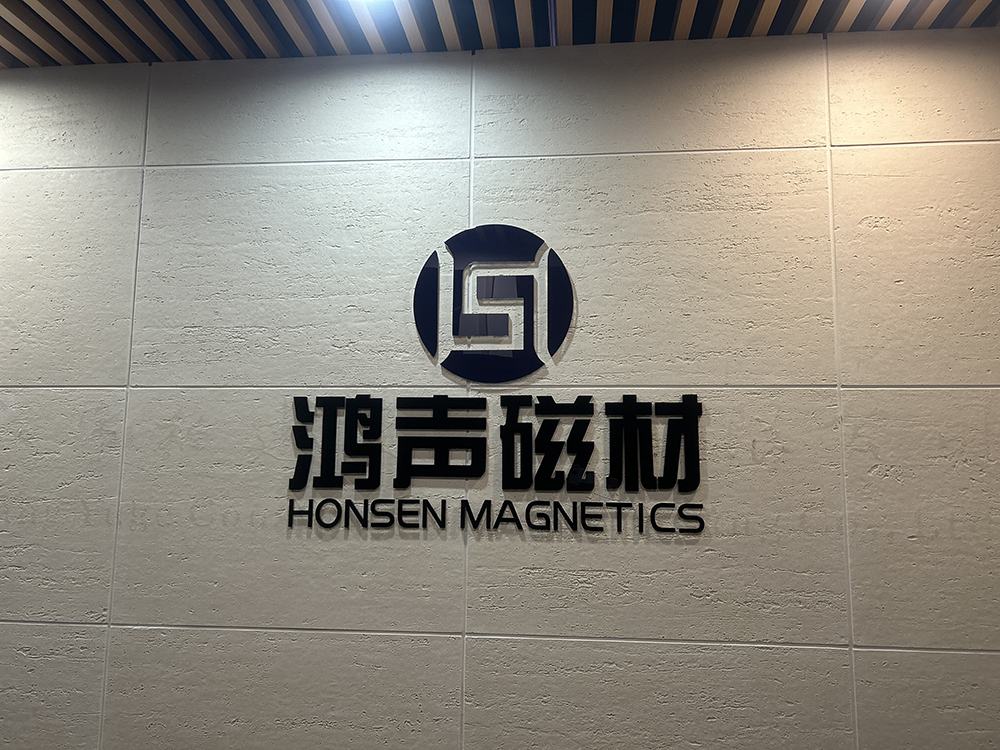
PRODUCTION FACILITIES
Our focus remains steadfast in providing our valued customers with avant-garde support and cutting-edge, competitive products that expand our market presence. Driven by revolutionary advances in permanent magnets and components, we are committed to driving growth and penetrating untapped markets through technological breakthroughs. Led by a chief engineer, our skilled R&D department leverages in-house capabilities, cultivates customer contacts, and anticipates changing market dynamics. Self-governing teams diligently oversee undertakings across the globe, ensuring that our research enterprise progresses steadily.

QUALITY & SAFETY
Quality management plays a central role in our business ethos. We believe that quality is not just a concept, but the essence and navigational tool of our organization. Our rigorous quality management system goes beyond paperwork and is deeply embedded in our processes. Through this system, we ensure that our products consistently meet our customers' specifications and exceed their expected standards.

PACKING & DELIVERY

TEAM & CUSTOMERS
The heart of Honsen Magnetics beats to a double rhythm: the rhythm of ensuring customer happiness and the rhythm of ensuring safety. These values go beyond our products to resonate in our workplace. Here, we celebrate every step of our employees' journey, viewing their progress as the cornerstone of our company's lasting progress.
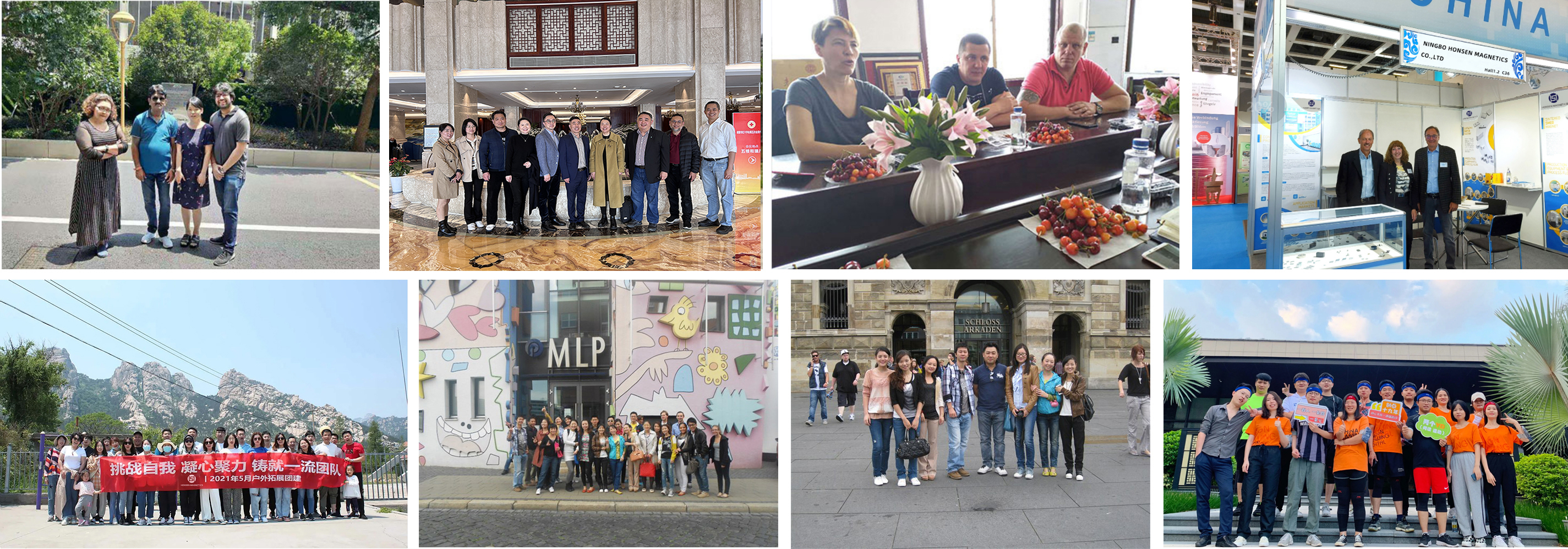
CUSTOMERS' FEEDBACK
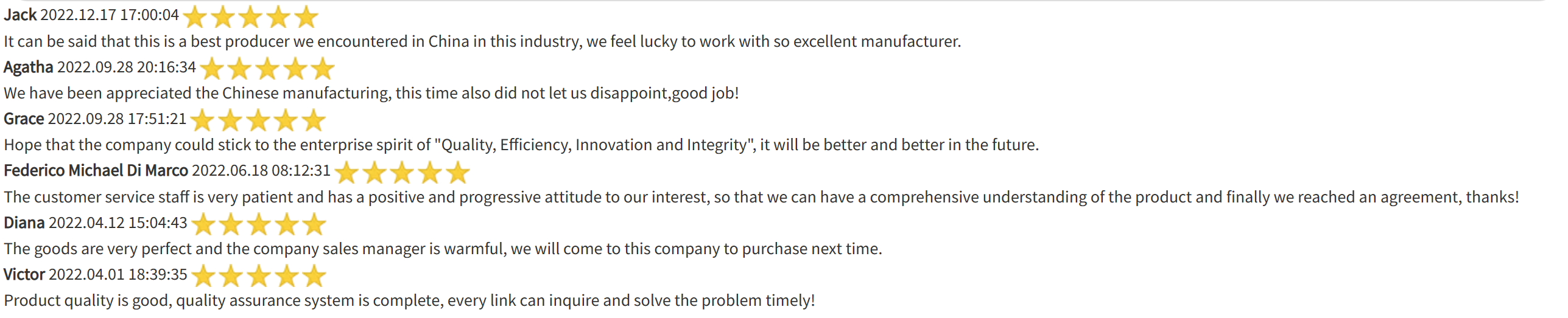